Силикатный бетон: применение, виды, характеристика
Бетонная смесь всегда используется в строительстве. Силикатный бетон — разновидность стройматериала, который характеризуется специфической примесью компонентов, что способствуют улучшению качества продукта и установлению нужных технологических свойств в конкретном целевом назначении.
Что собой представляет и состав
Традиционный силикатный бетон имеет вид бесцветного вещества, с прозрачной структурой, который не содержит цемента. Основной ингредиент состава — вяжущий ингредиент, чаще это известняк с примесью кремнеземнистого материала, что состоит из природного или синтетического пуццолана, кварцевого песка, металлургических отходов и древесной золы. Основной параметр ингредиента заключается в тонкости его помола, от этого показателя зависит качество бетона. В процессе смешивания образовывается химическая реакция, вследствие которой выводится гидросиликат кальция, что и способствует качественному скреплению монолита с наполнителями. Процедура осуществляется автоклавным способом ускорения. Такая технология приготовления — отличительное качество силикатного бетона от других смесей.
Виды и характеристика
Бесцементный бетон классифицируется по объемной массе и распределяется на такие разновидности:
- Тяжелый состав. Имеет крупный заполнитель в виде гравия, песка и щебня. Из такого класса смеси формируются крупногабаритные конструкции, прочность материала — 60 Мпа.
- Легкий. Основа состава — керамзит и вермикулит. Используется для возведения перегородок, внутренних стен.
- Ячеистый материал. Имеет пористую структуру. Характеризуется наличием пузырьков воздуха по периметру изделия. Рекомендован для эффекта теплоизоляции.
Бетон без цемента разделяется на виды, каждый из которых наделен уникальной технологической рецептурой приготовления и отличается индивидуальными специфическими свойствами:
- Специальный бетон. Его прочность достигает от 8 до 75 кг/м3.
- Конструкционный. В свою очередь разделяется на материалы, что имеют среднюю прочность, от 900 до 2500 кг/м3, на низкопрочные — от 2 до 5 и водоотталкивающие смеси.
Целевое применение
Силикатный бетон — редкий строительный материал. Используется для масштабного строительства и возведения бетонных конструкций с нуля. В качестве стройматериала для бытового ремонта к нему прибегают реже. Технические характеристики, параметры, предполагаемые ГОСТом, и свойства бесцементоной смеси позволяют использовать его в таких целях:
- Теплоизоляция. Рекомендуется ячеистый вид бетона. Благодаря искусственным порам, заполненным водой и технической пеной, он оказывается самым эффективным материалом для теплоизоляционного спектра.
- Строительный заполнитель. Силикатным бетоном рекомендуется заполнять промышленные, жилищные и сельские типы конструкций.
- Основа строительного объекта. Параметры бетонно-строительного материала позволяют применять его для возведения несущих стен и перекрытий крыш.
Посмотреть «ГОСТ 25214-82» или cкачать в PDF (134.6 KB)
При покрытии автомобильных трасс и магистралей используется тяжелый состав строительной смеси.Распространенный вид — тяжелый класс силикатного бетона. Он отличается от традиционного наличием кварцевого песка, что имеет мелкочастичную структуру. Виды тяжелого состава используются в таких целях:
- покрытие автомобильных трасс и магистралей;
- строительство подземных шахт и туннелей;
- заполнитель для шифера, черепицы, фундаментального блока, линейной стропильной системы;
- сооружение лестниц, потолочных и несущих балок;
- производство карнизных плит, деталей для возведения колонн, арок и маршей.
Каждый из видов материала предназначенный для конкретного эксплуатационного использования, единственный связывающий момент — свойства, близкие к параметрам цементной смеси.
От чего зависит качество?
Надежность силикатного бетона напрямую зависит от стандартов компонентов, входящих в состав смеси, а именно таких, как:
- процент входящего оксида кальция;
- размер зерен песка;
- уровень содержания минеральных соединений в вяжущем веществе.
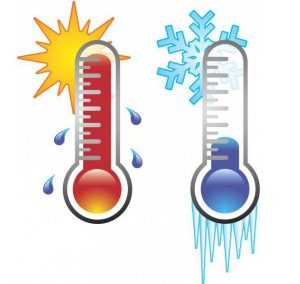
Кроме состава и способа приготовления бетона, за качество и сроки эксплуатации отвечают и технические моменты, такие как:
- правила укладки, применение;
- температурный режим;
- внешние факторы влияния;
- сроки выдержки;
- грамотная сфера приспособления материала.
Преимущества и недостатки
Плюсами силикатного бетона являются положительные показатели эксплуатации, а именно:
- Морозостойкость. Материал не боится циклов замораживания и оттаивания.
- Гидроустойчивость. Имеет водоотталкивающую структуру.
- Механическая устойчивость. Обладает повышенной стойкостью к силовым и весовым нагрузкам.
- Бюджетность. Имеет относительно небольшую себестоимость, и в странах СНГ участвует в национальных проектах «Доступное и удобное жилье для граждан».
- Теплопроводность и теплоизоляция. Для первого используются легкие составы, для второго — ячеистые.
- Максимальный эксплуатационный период. Минимальный срок использования от 70 до 100 лет.
Свойства силикатного бетона зависят от конкретного вида строительной смеси, которая определяется составом и целевым предназначением. К недостаткам материала относится один — низкая модуляционная упругость. Модуль угла изгибания силикатного бетона в два раза ниже чем в цементной смеси любого типа. Такой параметр имеет негативное воздействие в момент незаконченной выдержки, что грозит деформацией изделия и делает его дальнейшее применение невозможным. Силикатная основа опережает цементную более низким процентом ползучести, что уберегает конструкции от преждевременного разрушения.
znaybeton.ru
что это, состав и области применения.
Силикатный бетон – бесцементный строительный материал, вяжущими компонентами которого являются химические соединения кремнезема и гидрат оксида кальция. Они содержатся в кварцевом песке и дисперсных добавках. Для активации химического взаимодействия компонентов применяют обработку в автоклавах. Этот материал, благодаря невысокой стоимости, используется в крупномасштабном жилом строительстве. В отличие от цементного бетона, силикатный в индивидуальном домостроении практически не используется.
Сырьевые компоненты для силикатных бетонных смесей
Основное сырье, используемое при производстве этого материала, – известь. Для обеспечения требуемых эксплуатационных характеристик продукта необходима известь со следующими параметрами:
- процесс гидратации должен протекать со средней скоростью и с умеренным выделением тепла;
- материал должен иметь равномерный обжиг;
- содержание оксида магния (периклаза) – менее 5%;
- период гашения извести не должен превышать 20 минут.
Вторыми компонентами, использующимися вместе с известью, могут быть:
- кремнеземистые заполнители – тонко молотый кварцевый песок, доменный шлак, зола ТЭЦ;
- угольная или сланцевая зола;
- отходы производства керамзитовых заполнителей.
Наиболее распространенный заполнитель – кварцевый песок с мелким и средним зерном.
Внимание! Песок не должен содержать крупных глинистых включений, снижающих прочность и морозостойкость конечного продукта. Чем меньше фракция зерен кварцевого песка, тем выше прочностные характеристики и способность выдерживать циклы замерзания и оттаивания.
Примерный состав кварцевого песка:
- кремнезем – не менее 80%;
- глинистые включения – не более 10%;
- примеси слюды – до 0,5%.
Разновидности структур силикатных бетонов
В зависимости от применяемого заполнителя, автоклавные силикатные бетоны имеют различные структуры.
Плотные тяжелые бетоны
Изготавливаются с кремнеземистыми заполнителями и разделяются на мелко- и крупнозернистые. Чаще используются мелкозернистые смеси, при производстве которых используются малофракционные кварцевые пески. Плотность – 1800-2200 кг/м3. Преимущества этого строительного материала, по сравнению с цементным бетоном: однородная структура и меньшая стоимость. Прочностные характеристики материала прямо пропорциональны процентному содержанию кварцевого песка с мелким зерном. Тяжелый силикатный бетон востребован при изготовлении панелей перекрытий, колонн, лестничных маршей и площадок, возведении стен, производстве железнодорожных шпал с армирующими элементами.
Легкие
Изготавливаются с использованием пористых заполнителей – керамзита, перлита, пемзы, – имеющих форму щебня или гравия. В зависимости от плотности, легкие силикатные бетоны разделяют на группы:
- теплоизоляционные – плотность до 500 кг/м3, применяются в качестве утеплителя, обеспечивают оптимальный микроклимат, удерживают тепло и поглощают излишнюю влагу из внутреннего пространства;
- конструкционно-теплоизоляционные – 500-1400 кг/м3, подходят для изготовления внешних ограждающих конструктивных элементов;
- конструкционные – 1400-1800 кг/м3, востребованы при производстве ЖБИ.
Ячеистые легкие
Делятся на группы:
- Пеносиликатные. Состоят из тонкоизмельченной известково-кремнеземистой смеси, смешиваемой со специальной пеной. Обработка – автоклавная.
- Газосиликатные. Для их получения в известково-кремнеземистую смесь вводят алюминиевую пудру. По сравнению с пеносиликатными, имеют более широкую сферу применения в строительстве.
Основные характеристики
- Водопоглощение, зависящее от способа уплотнения, составляет 10-18%. Этот показатель снижают обработкой готовых блоков водоотталкивающими кремниевыми составами.
- Морозостойкость в общем случае – 50-100 циклов. По этому показателю силикабетонные смеси уступают цементным бетонам.
- Хорошие звукоизоляционные характеристики.
- Низкая себестоимость.
- Рабочий период – примерно 70 лет.
При использовании этого строительного материала, особенно видов с невысокой плотностью, необходимо принять меры по антикоррозионной защите арматуры. Вероятность коррозии высока при:
- постоянном высоком уровне влажности;
- отсутствии в составе смеси антикоррозионных компонентов;
- резких переменах климата.
Особенности производства силикабетонных смесей
Силикабетонные смеси и изделия из них производятся промышленным способом.
Основные этапы:
- подготовка сырьевых материалов – выделение требуемых фракций песка, термический обжиг известняка, дробление извести;
- помол сырьевых компонентов в шаровой мельнице;
- смешивание в бетоносмесителях;
- формирование бетоноизделий;
- автоклавная обработка при температуре 175-200°C;
- снижение температуры в автоклавном оборудовании или на воздухе.
Силикатный бетон: виды и технология производства
Силикатный бетон относится к группе безцементных бетонных растворов автоклавного твердения, приготовленных на базе известково-кремнеземистых вяжущих в соединении с разнообразными минеральными заполнителями. Качество этого вида бетонов регламентируется ГОСТ 25214-82 и должно соответствовать требованиям и нормам настоящего документа.
Общие сведения и основные характеристики силикатных бетонов
Силикатный бетон — это искусственный строительный материал, в котором главными цементирующими компонентами выступают химические соединения кремнезема и гидрата окиси кальция, содержащиеся в кварцевом песке или дисперсной добавке.
Эти компоненты значительно активизируются с применением автоклавной обработки, когда высокое давление водяного пара обеспечивает присутствие воды в жидком состоянии при повышенных температурах (>,100°С).
Силикатные бетоны представлены преимущественно мелкозернистой структурой. Заполнителями для таких растворов могут выступать кварцево-полевошпатные или традиционные кварцевые пески.
По структуре силикатные автоклавные бетоны могут быть:
- плотные тяжелые (заполнитель — кварцевый песок):
- плотные легкие (пористый заполнитель крупной или мелкой фракции)
- пористые бетоны
Легкий бетон на основе кремнеземистых компонентов
Легкий бетон изготавливают на пористых заполнителях — керамзите, перлите, шлаковой пемзе и других пористых материалах, применяемых в виде щебня или гравия. В качестве вяжущих используют те же компоненты, что и при изготовлении плотных тяжелых бетонов.
Учитывая плотность материалов и их конструктивные особенности, легкие бетоны подразделяются на три категории:
- Теплоизоляционные бетоны (плотность до 500 кг/м3, теплопроводность материала — 0,18 Вт/(м-°С)). Применяются для теплоизоляции перекрытий и покрытий общественных и промышленных зданий.
- Конструкционно-теплоизоляционные силикатные бетоны (плотность материала: 500–1400 кг/м3, теплопроводность изделий — 0,58 Вт/(м-°С). Применяются для производства наружных ограждающих бетонных конструкций (стеновые панели, блоки и др.).
- Конструкционные легкие бетоны (плотность изделий 1400–1800 кг/м3) применяются для производства армированных силикатобетонных конструкций и сборных железобетонных изделий.
Тяжелые бетоны с кремнеземистыми заполнителями
Тяжелые бетонные растворы, с учетом крупности заполнителя, делятся на мелкозернистые (песчаные) и крупнозернистые. Наиболее распространенными в этой группе считаются песчаные мелкозернистые смеси, состоящие из извести и мелкозернистого кварцевого песка.
Мелкозернистые тяжелые бетоны на кремнеземистых заполнителях, в сравнении с обыкновенными цементными, отличаются более однородной структурой, получаемой в результате плотной химической связи вяжущих и зерен заполнителя. А главный аргумент преимущества таких бетонов — это цена, которая намного ниже, чем у аналогичных по марке, цементных составов.
Силикатные тяжелые бетоны характеризуются плотностью от 1800 до 2200 кг/м3. Прочность растяжению–сжатию составляет 100–600 кг/см2, и может меняться в зависимости от состава смеси, объемного веса заполнителей и режима автоклавной обработки.
К примеру: бетоны на кремнеземистых заполнителях в период автоклавной обработки с содержанием извести 8–11% от общего объема заполнителя, при укладке смеси способом вибрирования, приобретают прочность равную 100–300 кг/см2. А при содержании в растворе15–30% мелкозернистого кварцевого песка, и при качественном уплотнении смеси с оптимальным режимом автоклавной термообработки, прочность того же материала возрастает до 400–600 кг/см2.
Пористые легкие бетоны
Материалы из ячеистых (пористых) бетонов делятся на пеносиликатные и газосиликатные. Пеносиликат производится путем смешивания специальной пены и тонкомолотой известково-кремнеземистой смеси с последующей обработкой силикатных изделий в автоклаве.
Для получения газосиликата, смешивают известково-кремнеземистую смесь с алюминиевой пудрой.
Наибольшее распространение получили газосиликатные смеси. При этом, производство газосиликатных изделий, в некоторых случаях, намного выгоднее чем изготовление аналогичных изделий из газобетона.
Известково-кремнеземистое вяжущее, присутствующее в составе газосиликатного раствора, позволяет качественно координировать процесс газообразования, что значительно влияет на плотность ячеистой структуры бетона, а впоследствии и на прочность готового изделия.
Свойства силикатных бетонов
Основные свойства силикатных бетонов представлены следующими показателями:
- Водопоглощение силикатных изделий, в зависимости от способа уплотнения бетонной смеси, равно 10–18%.
- Морозостойкость высокопрочного силикатного бетона доходит до 100 циклов и более.
- Высокая коррозийная стойкость – эти параметры незначительно отличаются от показателей цементного бетона.
- Термостойкость.
- Устойчивость к температурным и атмосферным воздействиям.
- Низкая себестоимость производства готовых изделий.
- Долговечность (до 70 лет).
Материалы для производства силикатных бетонов
Основным вяжущим компонентом в силикатном бетоне выступает тонкомолотая известь кипелка или известь-пушонка, которая в сочетании с заполнителями и составляет основное сырье для производства силикатных бетонов. После добавления воды и последующей тепловой обработки в автоклавах, силикатобетонная смесь превращаться в прочное бетонное изделие.
Известь, применяемая для производства силикатных смесей должна отвечать следующим свойствам:
- средняя скорость гидратации,
- умеренный экзотермический эффект,
- вся фракция должна быть одинаково обожженной,
- MgO менее 5%,
- время гашения извести — 20 мин не более.
Недожог известковой массы приводит к повышенному расходу материала. Пережог снижает время гидратации извести, что приводит к вспучиванию, появлению трещин на поверхности изделий и др.
Известь, применяемая для производства силикатобетона, обычно используется в виде тонкомолотых известковых смесей следующего состава:
- известково-кремнеземистые — соединение извести и кварцевого песка,
- известково-шлаковые (известь и доменный шлак),
- известково-зольные — топливная сланцевая или угольная зола и известь,
- известково-керамзитовые и другие подобные компоненты, получаемые из отходов промышленного производства пористых заполнителей,
- известково-белитовые вяжущие, получаемые при низкотемпературном обжиге известково-кремнеземистой сухой смеси и кварцевого песка.
В качестве кремнеземистых заполнителей используют следующие материалы:
- кварцевый молотый песок,
- металлургические (доменные) шлаки,
- зола ТЭЦ.
Наиболее часто в качестве заполнителей выступают кварцевые пески средней и мелкой фракции, которые по своему составу должны выглядеть следующим образом:
- 80% и более кремнезема,
- менее 10% глинистых включений,
- 0,5% и меньше примесей слюды.
Крупные включения глины в структуре кварцевого песка снижают морозостойкость и прочность силикатного бетона.
Тонкомолотый кварцевый песок оказывает значительное влияние на формирование высоких эксплуатационных свойств силикатных бетонов. Так, с повышением дисперсности частиц песка увеличивается морозостойкость, прочность и другие характеристики силикатных материалов.
При выборе составляющих для изготовления силикатного бетона необходимо знать следующее:
- Расход вяжущего увеличивается пропорционально увеличению прочности бетона.
- Снижение расхода вяжущих в составе силикатной смеси наблюдается при повышении дисперсности мелкого кварцевого песка, и увеличивается при повышении формовочной влажности силикатобетонного раствора.
- Дисперсность молотого кварцевого песка должна быть в 2,5 раза ниже дисперсности молотой извести.
Промышленное производство силикатобетонов
Промышленное производство силикатного бетона условно делится на несколько объемных этапов:
- подготовка необходимых материалов,
- приготовление известково-кремнеземистой смеси,
- формование силикатобетонных изделий,
- автоклавная обработка силикатобетона.
В состав предприятия, специализирующегося на производстве силикатобетонных изделий, входят следующие автономные отделения:
- отделение по приему материалов для изготовления силикатобетона,
- арматурное отделение,
- помольный цех,
- бетоносмесительное отделение,
- формовочный цех,
- автоклавное отделение,
- склад силикатобетонных изделий.
Примерная технологическая инструкция для изготовления силикатных изделий в заводских условиях представляется следующим образом:
- В помольном цехе измельчают, просеивают и сушат все необходимые составляющие известково-кремнеземистых вяжущих. Помол компонентов проводят в трубных или вибрационных мельницах.
- Затем материалы, при помощи пневмонасоса, поступают в бетоносмесительное отделение, где все необходимые компоненты дозируют и загружают в смеситель принудительного действия. Добавляют воду и перемешивают до получения однородной смеси. Для улучшения подвижности бетона, в его состав добавляют водные растворы пластификаторов.
- Готовая силикатобетонная смесь подается в бункер бетоноукладчика, с помощью которого она разливается в подготовленные формы. Время выдержки до распалубки готовых изделий должно составлять не менее 20 часов.
- После набора необходимой прочности, изделия складываются в штабели на вагонетки, и при помощи электропередаточного моста транспортируются в автоклавное отделение для термообработки.
Автоклавная обработка силикатных изделий
Процесс автоклавной обработки — последний и самый важный этап в производстве силикатобетонных изделий. Поэтому, для того чтобы понять саму сущность процесса автоклавной обработки, рассмотрим принципиальную схему работы автоклава.
Устройство автоклава
В автоклаве протекают сложные процессы, в результате которых силикатобетонные смеси превращаются в силикатобетонные изделия заданной плотности различной формы и назначения.
Автоклав для термообработки это горизонтально расположенный цилиндрический резервуар (Ø 2,6–3,6 м, длиной 20–40 м) с герметическими сферическими крышками. Сосуд оборудован манометром, регистрирующем давление пара, и предохраняющим клапаном, который автоматически открывается при повышении в резервуаре давления выше критического.
Внизу уложены рельсы для передвижения вагонеток с изделиями. Для снижения теплопотерь во время термообработки поверхность паропроводов и сама поверхность автоклава покрывается специальным теплоизоляционным составом. Помимо этого, автоклавы оборудованы устройствами для перепуска использованного пара в следующий автоклав и магистралями для сброса конденсата.
Общая схема процесса автоклавной обработки изделий
В подготовленный автоклав загружают отформованные силикатные изделия, и плотно закрывают сферические крышки. Затем, в устройство подают насыщенный пар.
Весь процесс автоклавной обработки материалов можно разделить на пять составляющих:
- Подача влажного пара с установленной в автоклаве температурой равной 100°С,
- Увеличение давления пара, и повышение температурного режима до технически необходимого минимума.
- Термическая выдержка изделий при максимально допустимой температуре и давлении.
- Постепенное снижение температуры до 100°С, и уменьшение давления пара до атмосферных показателей.
- Процесс остывания силикатных изделий до 18–20°С может проходить в автоклаве, либо на открытом воздухе.
Качество силикатобетонных материалов автоклавного твердения в значительной мере зависит от грамотного управления физико-химическими процессами, протекающими в автоклавах на различных этапах термообработки. Автоклавная термообработка материалов считается наиболее эффективным способом ускорения набора прочности бетонных изделий.
В заключение этой главы можно сделать следующий вывод: процесс производства силикатных изделий сложное и кропотливое занятие, требующее определенных знаний и специального оборудования. Приготовить силикатобетон в условиях строительной площадки своими руками можно, но получить изделия необходимого качества без автоклавной обработки практически нереально.
Поэтому, бетон силикатный и изделия из него, лучше приобретать на профильных предприятиях со специальным оборудованием и обученным персоналом. В этом случае, вы получаете гарантии качества приобретенных строительных материалов, и уверенность в том, что конструкция возведенная из этого материала, будет прочной и долговечной.
Изделия из силикатных бетонов
На сегодняшний день из силикатно-бетонных смесей производят следующие виды силикатных изделий:
- Крупные сборные железобетонные конструкции — плиты перекрытий, блоки, силикатные панели для стен фасадов.
- Из мелкоштучных изделий — рядовой, облицовочный кирпич, силикатные камни (блоки) и газосиликатные блоки для внутренних и наружных стен жилых и промышленных зданий.
Наибольшей популярностью в индивидуальном строительстве по праву пользуются силикатный кирпич и силикатобетонные изделия из пористых бетонов, которые и называют газосиликатными блоками.
Силикатный стеновой материал — кирпич
Силикатный кирпич — это стеновой материал, получаемый из смеси гашеной извести и кварцевого песка путем прессования, с последующим твердением в автоклавной установке под действием высоких температур и повышенного давления водяного пара (см. видео в этой статье).
Технология изготовления силикатного кирпича состоит из следующих технологических процессов:
- помол компонентов вяжущего (кварцевый песок и известь),
- дозирование компонентов (известь — 15–25%, кварцевый песок — 75–85),
- смешивание составляющих с добавлением воды, в результате которого происходит гашение извести и распределение компонентов смеси,
- прессование изделий под высоким давлением (30–40 Мпа),
- укладка изделий на вагонетку,
- автоклавная термообработка.
Расход компонентов вяжущего зависит от заданной плотности изделия. Смешивание компонентов проходит в двухвальном смесителе. Усреднение состава смеси и гашение извести проводят в агрегатах непрерывного или периодического действия.
Прессование кирпича выполняется при помощи револьверного пресса. Это станок карусельного типа, оборудованный зоной заполнения прессформы силикатным раствором, зоной прессования и выпресовки, а также зоной для съема сырца. Оптимальная влажность формовочной смеси 5–7%.
Затем силикатные изделия, уложенные на вагонетку, отправляют для сушки и твердения в автоклав.
Температура в автоклаве должна быть не ниже 175°С, оптимальное давление пара — 0,8 Мпа. Время автоклавной термообработки, для силикатного кирпича средней плотности, должно составлять 8–12 часов.
Силикатные кирпичи и камни могут быть следующих видов:
- одинарный кирпич полнотелый или пустотелый (250х120х65),
- утолщенный пустотелый кирпич (250х120х88),
- силикатные камни пустотелые (250х120х138).
Цвет рядового силикатного кирпича молочно-белый. Облицовочный кирпич может быть еще и цветным, окрашенным химически стойкими пигментами в различные декоративные цвета.
Для силикатного рядового кирпича и силикатных камней установлены следующие марки по прочности: 75, 100, 125, 150, 175, 200, 250, 300, марки по морозостойкости — F15, F25, F35, F50.
Марка по прочности для облицовочного силикатного кирпича не должна быть ниже 125, а по морозостойкости F35 и более. Водопоглощение силикатных изделий должно быть не более 6%.
Силикатные мелкоштучные изделия используют наравне с керамическим кирпичом для кладки стен надземной части жилых зданий и сооружений. Из–за недостаточной влагостойкости материала, его запрещается использовать для устройства фундаментов зданий даже с гидроизоляционным слоем.
Не допускается применение силикатных кладочных материалов для возведения зданий с влажным режимом эксплуатации (прачечные, бани и др.), а также использовать силикатные изделия для кладки печей и др.
Помимо известково-песчаных изделий еще производится известково-зольный и известково-шлаковый кирпич. В этих марках, вместо песка используют золы ТЭС или доменные металлургические шлаки. Свойства этих марок аналогичны характеристикам известково-песчаного силикатного кирпича.
Известково-зольные и известково-шлаковые силикатные изделия
Эти стеновые материалы — разновидность силикатного кирпича, в которых кварцевый песок подменен пористым металлургическим шлаком (известково-шлаковый) или топливной золой (известково-зольный).
Для изготовления известково-шлакового силикатного кирпича требуется 88–97% доменного шлака и 3–12% гашеной извести, а для производства известково-зольного материала нужно 75–80% топливной золы и 20–25% гашеной извести.
Зола и шлак являются дешевым силикатным сырьем, получаемым при сжигании бурого или каменного угля в котельных ТЭС и т.д. В период сгорания измельченного топлива, в топке остается крупная зола, а мелкие частички вместе с дымовыми газами уходят в дымоход, в котором установлены золоуловители. Полученная таким способом зола отправляется в отвал, а потом используется в производстве силикатных материалов.
Топливные золы и шлаки имеют в своем составе низкое содержание CaO (<,5%), и поэтому, при соединении с водой плохо твердеют. Но при введении извести они активизируются, а последующая термообработка в автоклаве дает возможность получить материалы высокой прочности.
Использование металлургических шлаков и топливных зол экономически выгодно, так как значительно снижается себестоимость готовых силикатных изделий.
Производство известково-зольного и известково-шлакового кирпича сравнимо с производством силикатного кирпича, а вот характеристики несколько отличаются от аналогичных свойств силикатного песчаного изделия:
- размер кирпича — 250х120х140,
- плотность материала 1400–1600 кг/м3,
- теплопроводность изделий 0,6 Вт/(м*К),
- прочность на сжатие (марки) — 75, 50 и 25,
- морозостойкость находится в тех же пределах что и у рядового силикатного кирпича.
Применяется известково-зольный и известково-шлаковый кирпич для устройства стен малоэтажных зданий.
Силикатные изделия из ячеистых силикатобетонов
Силикатные изделия пористой структуры характеризуются небольшим объемным весом и пониженной теплопроводностью. В этой главе рассмотрим производство и основные характеристики газосиликатных блоков, как наиболее популярных из всего ассортимента газосиликатных изделий, применяемых в индивидуальном строительстве.
Для приготовления газосиликатной смеси используются следующие материалы:
- портландцемент,
- известь-кипелка,
- алюминиевая пудра в качестве газообразователя,
- кварцевый песок,
- вода.
Технологическая инструкция производства пористых силикатных изделий представлена следующими операциями:
- Приготовление известково-кремнеземистого вяжущего.
- Сухая смесь поступает в смеситель, куда добавляют алюминиевую пудру и воду.
- Затем, готовую массу укладывают в подготовленные металлические формы.
- В формах происходит процесс вспучивания газосиликатной массы с образованием горбушки над границей формы. Горбушку срезают и отправляют на переработку. Окончание периода вспучивания массы должно совпадать с началом процесса схватывания вяжущего.
Газосиликатные блоки подразделяются на следующие категории:
- теплоизоляционные (плотность до 500 кг/м3, прочность на растяжение–сжатие 25 кг/см2),
- конструкционно–изоляционные (плотность 500–800 кг/м3, прочность на растяжение–сжатие 75 кг/см2),
- конструкционные (850 кг/м3 и более, прочность 75–150 кг/см2),
- средняя общая теплопроводность составляет 0,2 Вт/(м*К).
Основные размеры газосиликатных блоков представлены в таблице ниже (см. фото).
Свойства газосиликатных изделий:
- высокие теплоизоляционные свойства,
- морозостойкость,
- легкость монтажа и обработки газосиликатных материалов,
- высокая термостойкость,
- повышенная звукоизоляция,
- экологичность,
- долговечность.
Применяются газосиликатные блоки для кладки наружных и внутренних несущих стен, перегородок, а также могут служить теплоизоляционным материалом для утепления покрытия кровли, наружных стен и междуэтажных перекрытий.
Подсказки: влагостойкость силикатных изделий намного ниже, чем у аналогичных цементных. Поэтому, не рекомендуется применять газосиликатные блоки во влажных помещениях, и оставлять надолго наружные стены строения без гидроизоляции или дополнительной отделки фасада здания.
Как видим, бетон силикатный и изделия из него являются прекрасными и экономичными строительными материалами. По качеству силикатобетонные изделия не уступают изделиям из газобетона и тяжелого цементного бетона, а себестоимость их на 15–20 % ниже вышеназванных конкурентов.
craftroof.ru
СИЛИКАТНЫЙ БЕТОН — это… Что такое СИЛИКАТНЫЙ БЕТОН?
- СИЛИКАТНЫЙ БЕТОН
- СИЛИКАТНЫЙ бетон, бетон, получаемый термообработкой в автоклаве (при температуре 175 — 200шC) смеси известково-кремнеземистого вяжущего вещества, неорганических заполнителей (обычно песка) и воды. По свойствам близок к бетону на портландцементе. Широко используется для изготовления железобетонных конструкций (стеновых блоков и панелей, перекрытий, лестничных маршей и т.д.).
Современная энциклопедия. 2000.
- СИЛИКАГЕЛЬ
- СИЛИКАТНЫЙ КИРПИЧ
Смотреть что такое «СИЛИКАТНЫЙ БЕТОН» в других словарях:
СИЛИКАТНЫЙ БЕТОН — получают термообработкой в автоклаве (при температуре 175 200 .С) смеси на основе известково кремнеземистого вяжущего вещества, неорганических заполнителей и воды. По свойствам близок к бетону на портландцементе. Применяется для изготовления… … Большой Энциклопедический словарь
силикатный бетон — получают термообработкой в автоклаве (при температуре 175 200°C) смеси на основе известково кремнезёмистого вяжущего вещества, неорганических заполнителей и воды. По свойствам близок к бетону на портландцементе. Применяется для изготовления… … Энциклопедический словарь
силикатный бетон — silikatbetonis statusas T sritis chemija apibrėžtis Betonas, kurio rišamoji medžiaga – kalkių ir kvarcinio smėlio mišinio hidroterminio apdorojimo produktai. atitikmenys: angl. calcium silicate concrete; lime concrete; silicate concrete rus.… … Chemijos terminų aiškinamasis žodynas
Силикатный бетон — бетон, получаемый тепловлажностной обработкой (в Автоклавах) смесей, состоящих из известково кремнезёмистого вяжущего, неорганического заполнителя и воды. В процессе обработки силикатобетонного изделия (См. Силикатобетонные изделия) паром … Большая советская энциклопедия
СИЛИКАТНЫЙ БЕТОН — бетон, получаемый термообработкой в автоклавах смесей, состоящих из известково кремнезёмистого вяжущего заполнителя (обычно песка) и воды. Прочность на сжатие С. б. до 50 МПа, средняя (по объёму) плотн. 1800 2200 кг/м3. С. б. используется для… … Большой энциклопедический политехнический словарь
ячеистый силикатный бетон — akytasis silikatbetonis statusas T sritis chemija apibrėžtis Putų silikatbetonio ir dujų silikatbetonio bendras pavadinimas. atitikmenys: angl. cellular silicate; cellular silicate concrete rus. ячеистый силикат; ячеистый силикатный бетон;… … Chemijos terminų aiškinamasis žodynas
Бетон силикатный — – бетон, получаемый обработкой в автоклавах смесей, состоящих из известкового кремнезёмистого вяжущего, заполнителя и воды. [Терминологический словарь по строительству на 12 языках (ВНИИИС Госстроя СССР)] Бетон силикатный –… … Энциклопедия терминов, определений и пояснений строительных материалов
бетон силикатный — Бетон, получаемый обработкой в автоклавах смесей, состоящих из известкового кремнезёмистого вяжущего, заполнителя и воды [Терминологический словарь по строительству на 12 языках (ВНИИИС Госстроя СССР)] Тематики строительные изделия прочие EN lime … Справочник технического переводчика
Бетон — (франц. béton) искусственный каменный материал, получаемый из рационально подобранной смеси вяжущего вещества (с водой, реже без неё), заполнителей и специальных добавок (в некоторых случаях) после её формования и твердения; один из… … Большая советская энциклопедия
бетон — искусственный камень, получаемый в результате твердения рационально подобранной смеси вяжущего вещества, воды и заполнителей (песка и щебня или гравия). При правильном соотношении составляющих вяжущее вещество заполняет все промежутки между… … Энциклопедия техники
dic.academic.ru
Бетоны силикатные
Силикатные бетоны
Изготовление таких материалов основано на автоклавном твердении смеси из негашеной извести, кварцевого или обычного песка и другого заполнителя. Классификация производится по виду заполнителя, плотности, размеру фракций компонентов, структуре и пластичности раствора, а также области применения. Существует несколько видов силикатных бетонов:
- тяжелые в них заполнителем является песок смешанный с щебнем или гравием;
- легкие с наполнением из керамзита или аглопорита;
По ряду основных свойств силикатные бетоны очень близки к смесям на основе цемента. Для этого материала справедливы и зависимости свойств от технологических особенностей изготовления, выведенные для изделий из цемента. Он отличается более низкой устойчивостью к воде, которая может быть повышена путем введения специальных пропиток, карбонизацией или покрытием кремнийорганическими составами отталкивающими влагу. Еще один путь заключается во введении добавки из доменного шлака, которая позволяет образовать водостойкую гидросиликатную связку или малорастворимых соединений кальция. Такие составы хорошо противостоят не только воде, но и ряду других агрессивных сред.
Сейчас из автоклавного бетона получают несущие панели для внутренних помещений и перекрытий, а также крупные блоки для наружных стен. Из специальных составов изготавливают железнодорожные шпалы и шифер, в котором не содержится асбеста. Этот материал используется для строительства оснований шоссе, станций метрополитена и при прокладке шахт.
Ячеистые силикатные бетоны тоже получили широкое распространение. Они характеризуются значительным количеством искусственно созданных пор, заполненных газом или воздухом, которое может достигать 80% от общего объема. Такие материалы в свою очередь подразделяются на пенобетоны и газобетоны. Первые изготавливают смешиванием вяжущего с водой, кремнеземистым компонентом и пеной. Вторые добавлением в состав газообразователя: алюминиевой пудры или перекиси водорода.
Данные типы бетонов делятся на несколько видов:
- Теплоизоляционные, которые имеют плотность до 550 кг/М3;
- Конструктивно-теплоизоляционные, плотность которых находится в пределах от 550 кг/М3 до 950 кг/М3;
- Конструктивные более 950 кг/М3.
Для повышения прочности используется плотный зернистый кремнеземистый компонент, а перемешивание производится в специальном скоростном смесителе. Дисперсное армирование состава волокнистыми добавками увеличивает устойчивость на излом.
Свойства ячеистого бетона улучшаются после вибрационного воздействия на приготовленную смесь это способствует интенсификации процесса газовыделения и созданию однородной мелкопористой структуры.
Силикатный бетон с мелкозернистым наполнителем может иметь предел прочности до 50 МПа, а высокопрочные составы и более 80 МПа. Повышенная морозоустойчивость позволяет изделию перенести более 300 циклов замораживания с последующим оттаиванием без разрушения структуры. Существенный прирост в данном направлении дает добавка портландцемента. Её объем составляет не более 14% от количества известково-кремнеземистого вещества.
Тяжелые силикатные бетоны
Данный материал отлично зарекомендовал себя при проведении различных строительных работ, поэтому сегодня он широко используется во многих областях. Из такого раствора получают различные ЖБИ изделия и элементы конструкций. В первом случае используется тяжелые мелкозернистые смеси, основным компонентом которых является кварцевый песок. Данный материал обеспечивает плотность до 2300 кг/м3 и высокие прочностные характеристики. В ряде случаев изготавливается искусственный камень, выдерживающий до 100 МПа. Для увеличения нагрузочной способности силикатные бетоны смешивают на основе тонкомолотого кварцевого песка и уплотненной известково-кремнезем
vest-beton.ru
СН 529-80 «Инструкция по технологии изготовления конструкций и изделий из плотного силикатного бетона»
Искать все виды документовДокументы неопределённого видаISOАвиационные правилаАльбомАпелляционное определениеАТКАТК-РЭАТПЭАТРВИВМРВМУВНВНиРВНКРВНМДВНПВНПБВНТМ/МЧМ СССРВНТПВНТП/МПСВНЭВОМВПНРМВППБВРДВРДСВременное положениеВременное руководствоВременные методические рекомендацииВременные нормативыВременные рекомендацииВременные указанияВременный порядокВрТЕРВрТЕРрВрТЭСНВрТЭСНрВСНВСН АСВСН ВКВСН-АПКВСПВСТПВТУВТУ МММПВТУ НКММПВУП СНЭВУППВУТПВыпускГКИНПГКИНП (ОНТА)ГНГОСТГОСТ CEN/TRГОСТ CISPRГОСТ ENГОСТ EN ISOГОСТ EN/TSГОСТ IECГОСТ IEC/PASГОСТ IEC/TRГОСТ IEC/TSГОСТ ISOГОСТ ISO GuideГОСТ ISO/DISГОСТ ISO/HL7ГОСТ ISO/IECГОСТ ISO/IEC GuideГОСТ ISO/TRГОСТ ISO/TSГОСТ OIML RГОСТ ЕНГОСТ ИСОГОСТ ИСО/МЭКГОСТ ИСО/ТОГОСТ ИСО/ТСГОСТ МЭКГОСТ РГОСТ Р ЕНГОСТ Р ЕН ИСОГОСТ Р ИСОГОСТ Р ИСО/HL7ГОСТ Р ИСО/АСТМГОСТ Р ИСО/МЭКГОСТ Р ИСО/МЭК МФСГОСТ Р ИСО/МЭК ТОГОСТ Р ИСО/ТОГОСТ Р ИСО/ТСГОСТ Р ИСО/ТУГОСТ Р МЭКГОСТ Р МЭК/ТОГОСТ Р МЭК/ТСГОСТ ЭД1ГСНГСНрГСССДГЭСНГЭСНмГЭСНмрГЭСНмтГЭСНпГЭСНПиТЕРГЭСНПиТЕРрГЭСНрГЭСНсДИДиОРДирективное письмоДоговорДополнение к ВСНДополнение к РНиПДСЕКЕНВиРЕНВиР-ПЕНиРЕСДЗемЕТКСЖНМЗаключениеЗаконЗаконопроектЗональный типовой проектИИБТВИДИКИМИНИнструктивное письмоИнструкцияИнструкция НСАМИнформационно-методическое письмоИнформационно-технический сборникИнформационное письмоИнформацияИОТИРИСОИСО/TRИТНИТОсИТПИТСИЭСНИЭСНиЕР Республика КарелияККарта трудового процессаКарта-нарядКаталогКаталог-справочникККТКОКодексКОТКПОКСИКТКТПММ-МВИМВИМВНМВРМГСНМДМДКМДСМеждународные стандартыМетодикаМетодика НСАММетодические рекомендацииМетодические рекомендации к СПМетодические указанияМетодический документМетодическое пособиеМетодическое руководствоМИМИ БГЕИМИ УЯВИМИГКМММНМОДНМонтажные чертежиМос МУМосМРМосСанПинМППБМРМРДСМРОМРРМРТУМСанПиНМСНМСПМТМУМУ ОТ РММУКМЭКННАС ГАНБ ЖТНВННГЭАНДНДПНиТУНКНормыНормы времениНПНПБНПРМНРНРБНСПНТПНТП АПКНТП ЭППНТПДНТПСНТСНЦКРНЦСОДМОДНОЕРЖОЕРЖкрОЕРЖмОЕРЖмрОЕРЖпОЕРЖрОКОМТРМОНОНДОНКОНТПОПВОПКП АЭСОПНРМСОРДОСГиСППиНОСНОСН-АПКОСПОССПЖОССЦЖОСТОСТ 1ОСТ 2ОСТ 34ОСТ 4ОСТ 5ОСТ ВКСОСТ КЗ СНКОСТ НКЗагОСТ НКЛесОСТ НКМОСТ НКММПОСТ НКППОСТ НКПП и НКВТОСТ НКСМОСТ НКТПОСТ5ОСТНОСЭМЖОТРОТТПП ССФЖТПБПБПРВПБЭ НППБЯПВ НППВКМПВСРПГВУПереченьПиН АЭПисьмоПМГПНАЭПНД ФПНД Ф СБПНД Ф ТПНСТПОПоложениеПорядокПособиеПособие в развитие СНиППособие к ВНТППособие к ВСНПособие к МГСНПособие к МРПособие к РДПособие к РТМПособие к СНПособие к СНиППособие к СППособие к СТОПособие по применению СППостановлениеПОТ РПОЭСНрППБППБ-АСППБ-СППБВППБОППРПРПР РСКПР СМНПравилаПрактическое пособие к СППРБ АСПрейскурантПриказПротоколПСРр Калининградской областиПТБПТЭПУГПУЭПЦСНПЭУРР ГазпромР НОПРИЗР НОСТРОЙР НОСТРОЙ/НОПР РСКР СМНР-НП СРО ССКРазъяснениеРаспоряжениеРАФРБРГРДРД БГЕИРД БТРД ГМРД НИИКраностроенияРД РОСЭКРД РСКРД РТМРД СМАРД СМНРД ЭОРД-АПКРДИРДМРДМУРДПРДСРДТПРегламентРекомендацииРекомендацияРешениеРешение коллегииРКРМРМГРМДРМКРНДРНиПРПРРТОП ТЭРС ГАРСНРСТ РСФСРРСТ РСФСР ЭД1РТРТМРТПРУРуководствоРУЭСТОП ГАРЭГА РФРЭСНрСАСанитарные нормыСанитарные правилаСанПиНСборникСборник НТД к СНиПСборники ПВРСборники РСН МОСборники РСН ПНРСборники РСН ССРСборники ценСБЦПСДАСДАЭСДОССерияСЗКСНСН-РФСНиПСНиРСНККСНОРСНПСОСоглашениеСПСП АССП АЭССправочникСправочное пособие к ВСНСправочное пособие к СНиПСправочное пособие к СПСправочное пособие к ТЕРСправочное пособие к ТЕРрСРПССНССЦСТ ССФЖТСТ СЭВСТ ЦКБАСТ-НП СРОСТАСТКСТМСТНСТН ЦЭСТОСТО 030 НОСТРОЙСТО АСЧМСТО БДПСТО ВНИИСТСТО ГазпромСТО Газпром РДСТО ГГИСТО ГУ ГГИСТО ДД ХМАОСТО ДОКТОР БЕТОНСТО МАДИСТО МВИСТО МИСТО НААГСТО НАКССТО НКССТО НОПСТО НОСТРОЙСТО НОСТРОЙ/НОПСТО РЖДСТО РосГеоСТО РОСТЕХЭКСПЕРТИЗАСТО САСТО СМКСТО ФЦССТО ЦКТИСТО-ГК «Трансстрой»СТО-НСОПБСТПСТП ВНИИГСТП НИИЭССтП РМПСУПСССУРСУСНСЦНПРТВТЕТелеграммаТелетайпограммаТематическая подборкаТЕРТЕР Алтайский крайТЕР Белгородская областьТЕР Калининградской областиТЕР Карачаево-Черкесская РеспубликаТЕР Краснодарского краяТЕР Мурманская областьТЕР Новосибирской областиТЕР Орловской областиТЕР Республика ДагестанТЕР Республика КарелияТЕР Ростовской областиТЕР Самарской областиТЕР Смоленской обл.ТЕР Ямало-Ненецкий автономный округТЕР Ярославской областиТЕРмТЕРм Алтайский крайТЕРм Белгородская областьТЕРм Воронежской областиТЕРм Калининградской област |
files.stroyinf.ru
Силикатные бетоны
Изготовление таких материалов основано на автоклавном твердении смеси из негашеной извести, кварцевого или обычного песка и другого заполнителя. Классификация производится по виду заполнителя, плотности, размеру фракций компонентов, структуре и пластичности раствора, а также области применения. Существует несколько видов силикатных бетонов:
-
тяжелые в них заполнителем является песок смешанный с щебнем или гравием;
-
легкие с наполнением из керамзита или аглопорита;
-
ячеистые.
По ряду основных свойств силикатные бетоны очень близки к смесям на основе цемента. Для этого материала справедливы и зависимости свойств от технологических особенностей изготовления, выведенные для изделий из цемента. Он отличается более низкой устойчивостью к воде, которая может быть повышена путем введения специальных пропиток, карбонизацией или покрытием кремнийорганическими составами отталкивающими влагу. Еще один путь заключается во введении добавки из доменного шлака, которая позволяет образовать водостойкую гидросиликатную связку или малорастворимых соединений кальция. Такие составы хорошо противостоят не только воде, но и ряду других агрессивных сред.
Сейчас из автоклавного бетона получают несущие панели для внутренних помещений и перекрытий, а также крупные блоки для наружных стен. Из специальных составов изготавливают железнодорожные шпалы и шифер, в котором не содержится асбеста. Этот материал используется для строительства оснований шоссе, станций метрополитена и при прокладке шахт.
Ячеистые силикатные бетоны тоже получили широкое распространение. Они характеризуются значительным количеством искусственно созданных пор, заполненных газом или воздухом, которое может достигать 80% от общего объема. Такие материалы в свою очередь подразделяются на пенобетоны и газобетоны. Первые изготавливают смешиванием вяжущего с водой, кремнеземистым компонентом и пеной. Вторые добавлением в состав газообразователя: алюминиевой пудры или перекиси водорода.
Данные типы бетонов делятся на несколько видов:
-
Теплоизоляционные, которые имеют плотность до 550 кг/М3;
-
Конструктивно-теплоизоляционные, плотность которых находится в пределах от 550 кг/М3 до 950 кг/М3;
-
Конструктивные более 950 кг/М3.
Для повышения прочности используется плотный зернистый кремнеземистый компонент, а перемешивание производится в специальном скоростном смесителе. Дисперсное армирование состава волокнистыми добавками увеличивает устойчивость на излом.
Свойства ячеистого бетона улучшаются после вибрационного воздействия на приготовленную смесь это способствует интенсификации процесса газовыделения и созданию однородной мелкопористой структуры.
Силикатный бетон с мелкозернистым наполнителем может иметь предел прочности до 50 МПа, а высокопрочные составы и более 80 МПа. Повышенная морозоустойчивость позволяет изделию перенести более 300 циклов замораживания с последующим оттаиванием без разрушения структуры. Существенный прирост в данном направлении дает добавка портландцемента. Её объем составляет не более 14% от количества известково-кремнеземистого вещества.
Тяжелые силикатные бетоны
Данный материал отлично зарекомендовал себя при проведении различных строительных работ, поэтому сегодня он широко используется во многих областях. Из такого раствора получают различные ЖБИ изделия и элементы конструкций. В первом случае используется тяжелые мелкозернистые смеси, основным компонентом которых является кварцевый песок. Данный материал обеспечивает плотность до 2300 кг/м3 и высокие прочностные характеристики. В ряде случаев изготавливается искусственный камень, выдерживающий до 100 МПа. Для увеличения нагрузочной способности силикатные бетоны смешивают на основе тонкомолотого кварцевого песка и уплотненной известково-кремнеземистой смеси. Оказывает влияние и соответствующий режим автоклавной обработки.
Минусом конструкций, для которых используются силикатные бетоны, является низкий модуль упругости, который в несколько раз меньше, чем у цементных смесей. Очевидно, что данный параметр негативно сказывается на деформациях при кратковременном приложении значительных нагрузок. Кроме того, что ползучесть силикатного искусственного камня намного ниже, чем цементного.
Если рассматривать проблему полностью, то силикатные бетоны имеют то же значение суммарных деформаций, что и обычные, поэтому при замене тяжелой смеси на её силикатный аналог не требуется производить изменение структуры армирования.
Несмотря на то, что плотность данного материала часто оказывается ниже, чем у тяжелых смесей, специалисты все же используют его для отделки наружных конструкций промышленных сооружений и гражданских построек.
Особенности
Силикатные бетоныпо большей части представляют собой мелкозернистые смеси, которые твердеют в автоклаве. Отличие их от других составов заключается в том, что песок здесь не только заполнитель, но и один из компонентов вяжущего вещества известково-кремниземистого типа. Именно химическая реакция между известью и песком, которая происходит в автоклаве, обеспечивает создание твердого искусственного камня.
Использование кварцевого песка легко объяснимо: после того, как известь вступает в реакцию с кварцем, образуются соединения кальция – гидросиликаты. Они играют важную роль в процессе твердения материала и набора им прочности.
Силикатные бетоны изготавливаются из песков, содержание кремнезема в которых может достигать 80%. В ряде случаев допустимо использование аморфных его разновидностей, которые мало чем отличаются от кварца в ходе химической реакции. Данные вещества практически не представляют опасности для такого бетона, поскольку в результат проведения обработки в автоклаве большее количество щелочей связывается кремнеземом.
dombeton.ru