Процесс бетонирования
Организации, занимающиеся бетонными работами, пользуются многоразовыми опалубками из ламинированной фанеры, металла и т.п. Для того чтобы опалубка легко отделилась от застывшего бетона, непосредственно перед заливкой ее смазывают специи-альной смазкой для опалубки или эмульсией. Применять для этой цели отработанное масло запрещено из-за загрязнения окружающей среды и трудности в дальнейшей работе с бетонной поверхностью. В частном строительстве опалубку делают из досок и закрывают изнутри пленкой или рубероидом. Способ крепления пленки должен исключать ее загибание во время заливки бетона, обычно её пристреливают скобами через небольшие промежутки. Нельзя выгружать товарный бетон в дождь, снег, или когда внутри опалубки (котлована, траншеи) стоит вода, или тот же снег. Сначала нужно очис-тить место приема бетона.Перечислим распространенные методы бетонирования.
Первые два способа исполь-зуются при бетонировании фундаментов, два последних – при бетонировании колонн, стен, монолитных плит перекрытий. Подача бетона с лотка миксера непосредственно в опалубку – самый простой способ. Если миксеру обеспечена возможность подъезда на расстояние длины его лотка до места выгрузки, то бетонную смесь выгружают прямо в опалубку. Подача бетона по желобу. Когда близкий подъезд миксера по той или иной причине невозможен, бетонную смесь можно сгружать в деревянный желоб, который легко изготовить из досок на любой стройке. Для проталкивания бетона по лотку потребуются рабочие с лопатами, из расчета 1 человек на1 м длины лотка. Чем ниже подвижность бетона (осадка конуса), тем тяжелее его продвигать, даже в том случае, когда желоб имеет наклон в сторону разгрузки.Применение автобетононасоса. Если планируется привлечение бетононасоса, то следует заказывать бетон, рассчитанный на прокачку через бетононасос, он содер-жит добавки, увеличивающие текучесть при сохранении марки.Использование колокола. Колокол для бетонных работ представляет собой чашу с открывающимся сливным отверстием снизу. Колокол наполняют бетоном на земле, поднимают краном на место выгрузки и открывают сливное отверстие, после чего остается только разравнивать вытекающий бетон. Для бетонирования перекрытий над первым этажом и выше привлечение автокрана с колоколом обходится дешевле бетононасоса.Сразу после выгрузки бетона в опалубку его нужно уплотнить. Для этой цели используют вибратор. В частном строительстве при бетонировании фундаментов, перекрытий, столбов и т.д. применяют глубинный вибратор, у которого рабочий элемент погружается непосредственно в бетон. Радиус его действия составляет около 50 см, поэтому конструкцию уплотняют, опуская вибратор с промежутками 70-100 см. Это правило касается и глубины, т.е. вертикальные конструкции бетонируют послойно с вибрированием каждого слоя. Когда вибратора нет, можно попытаться уплотнять бетон путем штыкования отрезком арматуры. Но в любом случае вибратор обеспечивает гораздо лучшее качество бетонирования. Побочный эффект вибрирования – саморастекание бетона по уровню горизонтали.Технология выравнивания зависит от вида бетонируемой конструкции. Если конструк-ция имеет относительно небольшую площадь (ленточный фундамент, стены, колонны), то проще всего смонтировать опалубку, выравнивая ее верх по нужному уровню. Если опалубка ставится без выравнивания, то отметку уровня можно провести внутри нее, например, натянув шнур. При бетонировании плиты перекрытия или фундамента для контроля уровня используют маячки. Чаще это отрезки арматуры, выставленные в одной плоскости. При бетонировании полов, где требуется высокая точность, поверхность выравнивают по маякам из направляющих профилей, уложенных в плоскости пола.Как только бетон залит, уплотнен и выровнен в соответствии с проектом, наступает черед позаботиться об условиях его созревания. Для этого нужно не допустить высыхания (а зимой – замораживания) бетона, особенно в первые дни, а также защитить его от атмосферных осадков на период схватывания. Для защиты от высыхания и осадков свежеуложенный бетон закрывают полиэтиленовой пленкой. При температуре выше +5 °С этого достаточно.Технология бетонирования в зимнее время подразумевает подогрев бетона – электродный или при помощи тепловой пушки под каким-либо тентом. В первые трое суток созревание бетона происходит с выделением теплоты. Если имеется возможность устроить теплоизолированное укрытие конструкции, при котором температура бетона не падает ниже +5°С до набора 50% расчетной прочности (а это примерно 3 суток), дополни-тельный обогрев можно не устраивать. Если ставился подогрев, то его прекращают также по набору 50% прочности (как правило, те же 3 дня). После снятия подогрева бетон может замерзнуть – в этом нет ничего страшного, процесс набора прочности возобновится с повышением температуры выше нулевой отметки.В жаркую погоду бетон нужно ежедневно увлажнять, даже когда он укрыт пленкой: пленка снимается, поверхность проливается водой и снова укрывается. И так 5-7 дней. По прошествии недели укрытие можно снимать и демонтировать опалубку, если бетони-руемая конструкция не является перекрытием. Реально, с фундаментов снимают укрытие и опалубку даже на 3-4 день от заливки. Распалубку висячего перекрытия делают после набора 80% прочности. После распалубки конструкцию можно нагружать, не забывая о 28 сутках для полного набора прочности.
n-sk54.ru
земляные работы, приготовление и способы
Фундамент является неотъемлемой частью любого здания и сооружения. При его возведении важно не допустить технологических ошибок, ведь невнимательность и несоблюдение этапов строительства, способны привести к серьезным последствиям. Несмотря на серьезную ответственность, возведения фундаментов – это легкий процесс, с которым справится даже новичок. Бетонирование фундамента позволит получить прочную, надежную основу для зданий и сооружений, которая прослужит не один десяток лет. Но чтобы конструкция получилась с требуемыми прочностными характеристиками, следует обратить внимание на основные тонкости, которые присутствуют в процессе бетонирования.
Какие нужны материалы и инструменты?
Чтобы возвести бетонный фундамент, потребуются следующие инструменты и материалы:
- сварочный аппарат;
- терка;
- колышки;
- стальные прутья;
- бетономешалка или пустая емкость для приготовления раствора;
- лопата;
- веревка или шнур для разметки;
- тяпка;
- строительный уровень;
- цемент;
- песок;
- щебень;
- вода;
- брусья для возведения опалубки.
Земляные работы
Перед бетонированием подготавливают строительный участок и проводят комплекс мероприятий, необходимых для строительства фундамента. Первый этап включает в себя земляные работы. Для этого понадобятся колышки и веревка, которыми сделают разметку местности. После того как территория размечена, приступают к рытью траншеи. Глубину траншеи делают такой, чтобы она была больше глубины промерзания почвы на 30 сантиметров. Дно вырытой траншеи заполняют слоем песка или щебня.
Процесс возведения фундамента хоть и легкий, но все же требует определенных силовых нагрузок и времени, поэтому рекомендуют нанять еще несколько человек, которые помогут ускорить строительство. Облегчить работу можно, воспользовавшись услугами специальной техники. Трактор качественно и быстро выроет траншею даже в местах с твердым грунтом.
Вернуться к оглавлениюСоздание опалубки
В качестве основы под бетонную смесь устанавливают опалубку из деревянных досок или сборных щитов. При монтаже опалубки следует придерживаться следующих тонкостей:
- Части опалубки должны быть точно установлены и проверены строительным уровнем, который исключит перекосы и наклоны основы.
- Качество поверхности досок, а также наличие в возводимой конструкции щелей способны повлечь за собой ряд неприятных последствий. Поэтому возможные зазоры между досками устраняют еще до момента кладки рабочей смеси.
- Для достижения требуемой жесткости опалубки используют доски толщиной не меньше пяти сантиметров, которые способны выдержать большие нагрузки в процессе бетонирования конструкции.
- Чтобы придать опалубке повышенную жесткость, следует применять больше подкосов, располагая их с меньшим шагом.
- Перед тем как возводить опалубку, нужно вырыть траншею, засыпать ее и выровнять.
Установка опалубки начинается с забивки расположенных по всему периметру колышков в поверхность грунта. Далее приступают к крепежу досок с помощью гвоздей. Важно следить за ровностью возводимой конструкции, иначе перекосы отразятся на фундаменте. Демонтаж опалубки проводится после того как бетон полностью высохнет. Произойдет это через пару дней после кладки рабочей смеси.
Вернуться к оглавлениюПриготовление раствора
Чтобы обеспечить фундаменту высокую прочность, следует приготовить бетонный раствор с высокими качественными характеристиками. Цемент приобретают марки не ниже М-200. Для его приготовления понадобятся:
Для изготовления смеси нужно засыпать в бетономешалку сухие ингредиенты: три части песка, одну часть цемента и пять частей щебня. Сухие компоненты перемешивают и заливают водой, воды должно быть столько, чтобы получить раствор консистенции, напоминающей густую сметану. Перемешивание компонентов смеси в бетономешалке займет около пяти минут, если возможность приобретения такого оборудования отсутствует, тогда разводят рабочую смесь в емкости большого объема. Но тогда стоит учитывать, что приготовление раствора без специального оборудования займет много времени.
Вернуться к оглавлениюДелать бетонную смесь нужно непосредственно перед началом заливки фундамента.
Способы бетонирования
При бетонировании основы под здания и сооружения следует провести армирование стальными прутьями, диаметр которых 0,8-1,2 сантиметра. Из стальных прутьев конструируют сетку, соблюдая при этом размеры ячейки – 150х150 миллиметров. Бетонируем конструкцию только после того, как установлена армирующая сетка в полость опалубки. Кладка бетонного раствора может выполняться двумя способами:
- Ручной способ. Фундаменты, возведенные вручную, подразумевают заливку готового раствора несколькими людьми. В данном случае на строительной площадке должны находиться две бетономешалки, которые подают цемент с двух сторон.
- При помощи миксера. Кладка бетонной смеси с использованием миксера осуществляется в несколько раз быстрее ручного способа. Этот способ возведения фундамента является дорогостоящим, но с лучшим готовым результатом.
Ручной способ
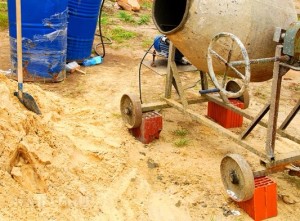
Чтобы бетонировать небольшие сооружения, применяют ручной способ, для осуществления которого потребуется бригада из нескольких рабочих. При попытке бетонировать в одиночку, можно навредить строительному процессу и все труды будут напрасными.
Также следует приобрести две бетономешалки, которые устанавливают с двух сторон объекта бетонирования. На каждое оборудование назначается три человека. Процесс заливки раствора из песка, цемента и щебня должен осуществляться быстро, так как бетонный состав способен быстро набирать прочность. Бетонный раствор подают по всему периметру фундамента толщиной до 40 сантиметров.
После заливки смеси ее следует тщательно утрамбовать глубинным вибратором. Уплотнение позволит избавиться от пузырьков воздуха в смеси и распределить ее по всей глубине конструкции. Далее приступают к укладке последующего слоя бетонного раствора, который также следует уплотнить. Заливка каждого нового слоя осуществляется спустя два часа после того, как закончили бетонировать предыдущий. Заливка последнего слоя требует особой внимательности, а именно придание поверхности особой ровности. Сделать ровный слой можно с помощью строительного уровня или других специальных приспособлений для выравнивания массивной поверхности.
Залитый бетон достигнет своих прочностных характеристик спустя месяц, на протяжении которого важно обеспечить оптимальные условия для застывания бетонного раствора. Чтобы предотвратить воздействие прямых солнечных лучей и атмосферных осадков на бетон, следует накрыть его изолирующими материалами.
Вернуться к оглавлениюПри помощи миксера
Заливка фундамента с помощью миксера подразумевает использование транспортного средства, которое осуществит заливку бетонного раствора по всему периметру фундамента в короткие сроки. Такой способ более затратный, чем ручной, поэтому перед выбором способа бетонирования следует определить для себя приоритетные аспекты.
Заливка бетонного раствора с применением миксера включает в себя подачу бетона специальными желобами в опалубку. Стоит учитывать скорость подачи раствора и успевать выравнивать вибратором или тряпкой залитую поверхность.
Вернуться к оглавлениюУстройство рабочих швов
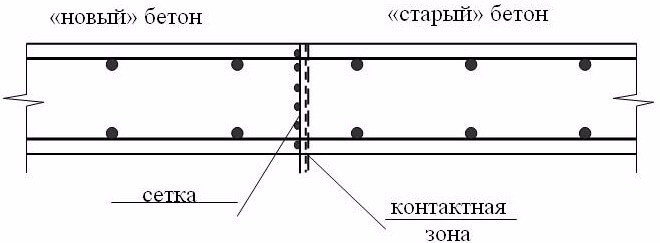
Заливку фундаментов бетонным раствором рекомендуется осуществлять без продолжительных перерывов. Укладка последующих слоев смеси не должна иметь перерыв более трех часов. Но зачастую придерживаться таких правил не получается и тогда нужно организовать устройство рабочих швов.
Рабочие швы являются границей между заливаемыми бетонными слоями, и при их изготовлении следует придерживаться технологического процесса. Если технология будет нарушена, то фундамент для зданий и сооружений не приобретет нужных качественных характеристик.
Устанавливая рабочие швы, важно добиться максимальной адгезии бетонных слоев со швами. Для этого затвердевшую поверхность следует подготовить для проведения последующих работ. Поверхность очищают от пыли, снега, мусора или воды. Далее удаляют цементное молочко, которое образуется на затвердевшем растворе. Цементное молочко образует пленку, которая имеет рыхлую непрочную структуру, что приводит к снижению адгезии раствора с затвердевшим слоем. Удаление пленки проводят с помощью водяной или воздушной струи, которую подают под высоким давлением. Таким образом, осуществляется удаление пленки с затвердевшей поверхности из бетона. Помимо удаления пленки струей с высоким давлением, используют фрезеровочные машинки. Разрушить цементную пленку можно кислотой, которую наносят на твердый слой и оставляют на несколько часов.
К укладке последующих слоев бетонного раствора приступают только после удаления пленки с застывшей поверхности. Далее проводят утепление и гидроизоляцию швов, что позволит предотвратить преждевременное разрушение основы зданий и сооружений.
Вернуться к оглавлениюЗаключение
Для качественного и прочного возведения фундамента следует придерживаться технологии производства и последовательности этапов. Соблюдение всех правил и рекомендаций по заливке бетонным раствором приведет к созданию надежного основания для зданий и сооружений, исключит необходимость в создании рабочих швов.
Но если все-таки создание швов неизбежно, тогда следует тщательно подготовить поверхность перед тем, как приступать к укладке бетонного раствора.
kladembeton.ru
Процесс бетонирования монолитных конструкций
Учитывая определенные сложности при закладке раствора в монолитные конструкции, лучше всего подыскать проверенную организацию с опытными сотрудниками. Профессионалы СК Синмар выполнят высококачественные бетонные работы любой сложности на высоком уровне по демократичной стоимости.
Особенности бетонирования монолитных конструкций
Бетон является искусственным камнем, полученным методом смешивания связующих составляющих (вода, цемент, песок) и наполнителя (щебень либо гравий), а также добавки пластификаторов, которые повышают эластичные и пластичные характеристики раствора. При осуществлении бетонных работ следует полностью придерживаться государственных стандартов и действующего законодательства.
крошение бетонного массива;
возникновение концентраторов напряжения;
искривление строения;
ухудшение защитного слоя
скол либо откол бетонного массива.
Для эффективного бетонирования монолитных конструкций необходимо подобрать подходящий тип опалубки, которая может быть съемной или несъемной. Первая их них делается отдельно для всех разработок, полностью повторяя форму сооружения. Щитовые элементы скрепляются гайками, шпильками и шайбами. Благодаря использованию гофрированных трубок можно без особого труда демонтировать опалубку при полном затвердевании раствора. Несъемная опалубочная система – форма из пенополистирола, которая крепится профилями и устанавливается на основании. Надежное крепление позволяет исключить возможную утечку бетонной смеси. Данный тип опалубки не снимается после заливки раствора.
При возведении монолитных сооружений следует определиться с материалом для изготовления опалубочной системы. Они бывают следующими:
Дерево. Один из наиболее применяемых типов опалубки. Ее производят их хвойного либо лиственного дерева, толщина которого более 20 мм.
Металлические листы. Их используют как для съемной, так и для несъемной опалубочной системы.
Фанера. Данный материал чаще всего применяется для производства стен, колон, лестниц. Хорошо подходит для строительства загородных домов.
Синтетические материалы. Их разнообразие все время увеличивается, но зачастую применяют стеклотекстолит, пенопласт, стеклоткань.
Древесностружечная плита. Используют материал, толщина которого составляет 20 мм, для изготовления стен и колон.
Квалифицированные специалисты СК Синмар предлагают клиентам возвести долговечные промышленные фундаменты с использованием качественных стройматериалов по доступной стоимости. При создании проекта мы продумаем тип и глубину заложения основания, а также выполним расчет предстоящих расходов. Обязательно проведем топографические, геодезические, геологические, гидрогеологические исследования на строительном участке. Изучим грунт, глубину его промерзания и уровень залегания грунтовых вод. Исходя из результатов выполненных изысканий, мы принимаем решение по оптимальному выбору фундамента для будущего сооружения.
Наши сотрудники уделяют пристальное внимание заливке бетонного раствора и строго соблюдают все технические тонкости при закладке основания. Для сухой и устойчивой почвы мы выполним монолитный фундамент с использованием мощного арматурного каркаса. В случае строительства высотного сооружения займемся устройством экономичного свайного основания. Зачастую мы используем их на водянистой почве либо в заболоченных районах. При монтаже всех видов фундамента учитываем проектные особенности, параметры стройплощадки и актуальные нормативные требования.
Процесс бетонирования монолитных конструкций
При проведении бетонно-строительных работ наши сотрудники учитывают степень нагрузки на почву и климатические особенности местности. Мы осуществляем заливку раствора в полном соответствии со строительными нормами и созданным проектом будущего сооружения. Процесс бетонирования монолитных конструкций сотрудниками СК Синмар состоит из следующих стадий:
Подготовительные работы. Мы займемся подбором качественного бетона и организуем его оперативную доставку. Заказывая данный материал, мы тщательно проанализируем параметры его морозостойкости, водопроницаемости, подвижности. В зависимости от назначения сооружения, вида армирования и метода бетонирования наши специалисты укажут марку и процентное соотношение мелкого и крупного заполнителя. До устройства опалубки уберем все крупногабаритные грузы и очистим участок от различного мусора и материалов.
Устройство опалубочной системы. Наши сотрудники смонтируют опалубку и непосредственно перед укладкой бетонной смеси обработают ее с помощью специальной смазки или эмульсии для легкого снятия после завершения работ.
Монтаж арматурного каркаса. Применяемая арматура придает требуемую форму строящемуся сооружению и позволит ему приобрести максимальные показатели надежности и долговечности.
Приготовление раствора. Производство небольших монолитных блоков выполним на месте строительства, а бетонную смесь заказываем на заводе-изготовителе и централизованно доставляем на объект.
Транспортировка бетона к месту заливки. Перевозка раствора на строительный объект осуществляем бетононасосами либо автобетоносмесителями. При транспортировке принимаем меры для защиты бетонной смеси от атмосферных осадков, ветра и солнца. Зимой используем специальной утепленный тип транспорта, чтобы раствор не заморозился.
Заливка бетонной смеси в опалубочную систему. Для правильного спуска бетона мы придерживаемся всех правил и требований, поэтому сбрасываем раствор в армированные конструкции при высоте менее 2 м. В других случаях применяем виброжелобы, которые обеспечивают постепенное сползание бетонной смеси без расслоения. Для бетонирования применяем специальный миксер, выгружающий раствор непосредственно в опалубочную систему. В некоторых случаях используем колокол, который наполняем смесью на земле и поднимаем с помощью крана на необходимую высоту, выгружаем и аккуратно разравниваем вытекающий раствор. Бетон укладываем горизонтальными слоями с одинаковой толщиной, исключая появление разрывов. Качественное уплотнение осуществляется при помощи поверхностных вибраторов. В результате раствор становится более пластичным и попадает во все незаполненные места. После вибрирования мы тщательно выравниваем бетон и оставляем застывать.
Уход за бетоном во время его твердения. В течение первых 5 дней застывания мы поддерживаем влажное состояние раствора, периодически поливая его водой. Для защиты от воздействия прямых солнечных лучей укроем бетон тканью, опилками либо песком, поддерживая данные материалы во влажном состоянии. На период твердения мы не допускаем передвижение людей или техники по поверхности.
Распалубливание бетона. Перед началом данных работ мы проводим тщательный осмотр всех конструкций. Наши специалисты испытают бетон на прочность, осуществив лабораторные исследования с использованием ударно-импульсных и звуковых устройств.
Распалубливание, зачастую, производится через 10-12 суток после закладки раствора в зависимости от набора бетоном необходимых прочностных характеристик, а также назначения конструкций и их веса.
Почему выгодно заказать бетонирование монолитных зданий в СК Синмар?
Для осуществления бетонирования в штате компании имеются строительные бригады, которые обеспечены современным инструментом, приспособлениями и оборудованием. Каждый этап заливки раствора выполняется под полным контролем наших специалистов, имеющих соответствующее профильное образование и немалый опыт проведения бетонных работ. Мы проведем бетонирование монолитного сооружения в строгом соответствии со строительными нормативными документами, так как любые отклонения от них могут привести к серьезным нарушениям и дополнительным затратам для клиента.
Заказывая услугу бетонирования монолитных конструкций в СК Синмар, клиент получает ряд значительных преимуществ:
оперативное оформление заказа;
применение новейших методов проектирования;
выполнение всех обязательств в заданные сроки;
полное соответствие работ установленным стандартам качества;
выгодную стоимость бетонных работ;
монтаж с последующей гарантией;
поставка качественных материалов от проверенного производителя;
индивидуальный подход к каждому заказчику.
Обратитесь в СК Синмар и заказывайте высококачественное монолитное строительство под ключ с использованием современных материалов и новейших технологий. Наши сотрудники в полной мере учитывают требования, пожелания и архитектурные идеи клиента. Мы проведем инженерно-геологические исследования района, благодаря которым определим оптимальное месторасположение будущего объекта. Осуществим расчет прочностных параметров строения и подберем подходящие места для подвода необходимых коммуникационных сетей.
Займемся устройством каркаса и подходящей опалубочной системы, а также осуществим правильную заливку бетонной смеси. Все монолитные работы выполняются под полным контролем инженеров технического надзора, которые не допускают нарушений технологических процессов и установленных стандартов подрядными организациями.
Мы предлагаем клиентам приемлемую стоимость возведения сооружений из монолита и осуществляем сдачу здания в сроки, четко установленные клиентом в договоре. Наши специалисты выполнят точный расчет количества требуемых стройматериалов и различных конструкций, полностью исключая непредвиденные затраты для заказчика.
При появлении любых вопросов, связанных с монолитным строительством под ключ, оставьте оформленную заявку на сайте для бесплатной консультации менеджеров СК Синмар.
sksinmar.ru
Процесс — бетонирование — Большая Энциклопедия Нефти и Газа, статья, страница 1
Процесс — бетонирование
Cтраница 1
Процесс бетонирования в целях обеспечения необходимой монолитности конструкции должен происходить непрерывно. Поэтому при бетонировании следует избегать перерывов в подаче бетона. В случае же перерыва при укладке новых порций бетона, необходимо обеспечить условия для схватывания укладываемого бетона с затвердевшим путем очистки, насечки и смазывания цементным раствором поверхности соприкосновения. [1]
Процесс бетонирования в целях обеспечения необходимой монолитности конструкции должен происходить непрерывно. Поэтому прп бетонировании избегают перерывов в подаче бетона. В случае же перерыва при укладке новых порций бетона необходимо обеспечить условия для схватывания укладываемого бетона с затвердевшим путем очистки, насечки и смазывания цементным раствором поверхности соприкосновения. [2]
Процесс бетонирования сваи цикличный. В скважину подают порцию бетонной смеси, которая образует в обсадной трубе столб ( пробку) высотой не более 1 м; смесь уплотняют трамбовкой, одновременно приподнимая лебедкой обсадную трубу. Выходя из трубы, бетонная смесь плотно забивает скважину и, вдавливаясь в окружающий грунт, образует утолщение сваи. После этого цикл повторяется. Работа продолжается в такой же последовательности до полного удаления обсадной трубы. [3]
Процесс бетонирования фундаментов имеет свои особенности и трудности, обусловленные в основном тремя причинами: насыщенностью арматурой, сложным очертанием элементов при наличии в них множества отверстий и вырезов и большой высотой подачи бетонной смеси для бетонирования колонн и низа горизонтальных элементов. Эти причины препятствуют нормальному прохождению бетона в элементы фундамента. [4]
Процесс бетонирования пустотелых элементов начинается с нижней стенки ( дна) и ведется равномерно по горизонтали. Вибрирование высокочастотным вибратором осуществляется послойно ( толщина 15 — 20 см) в течение 10 — 15 мин. Нижняя половина пустотелого элемента заполняется бетоном в три приема. Затем переходят к верхней части и заполняют ее бетоном также в три приема, подвергая вибрации каждый слой. При этом поверхностные вибраторы включаются лишь при заливке верхней половины элемента. Бетонирование заканчивается за одну смену и производится бригадой из 3 чел. Таким образом, на подготовку к бетонированию элемента и бетонирование, а также распалубку требуется 9 — 10 чел-дней. Сплошные элементы изготовляются с применением пропарки. Сборка каркаса производится вне камеры; поддон опалубки устанавливается в камере и на него ставится собранный каркас. Бетонирование производится в камере. На рис. 7 — 3 показано извлечение готового элемента из пропарочной камеры. На подготовку к бетонированию сплошного элемента и бетонирование требуется 6 — 7 чел-дней. Пустотелые элементы лишь незначительно более трудоемки в изготовлении, чем сплошные. [5]
В процессе бетонирования для последующего крепления к конструкциям разного оборудования и механизмов в бетон закладывают специальные закладные части, болты и вкладыши. [7]
В процессе бетонирования опалубка поднимается на 40 — 50 см и к его окончанию заполняется на всю высоту. [9]
В процессе бетонирования периодически проверяют положение шаблона анкерных болтов и закладных, частей. Шаблоны разрешается снимать не раньше чем через сутки после окончания бетонирования. Все дефектные места и раковины зачищают и заделывают цементным раствором, после чего на подземную часть фундамента наносят гидроизоляцию. [10]
В процессе бетонирования следует постоянно наблюдать за состоянием опалубки. При обнаружении деформации или смещения опалубки бетонирование сразу же прекращают. Во время дождя и снега бетонируемый фундамент должен быть надежно защищен от попадания атмосферных осадков; случайно размытый участок бетона удаляют и заменяют свежей смесью в соответствии с общими правилами бетонирования. Укладку бетонной смеси в конструкцию сопровождают соответствующими записями в журнале производства бетонных работ. [11]
В процессе бетонирования колодца ставят ерши для кронштейнов и серег или же на местах, где они должны быть установлены, вставляют деревянные пробки, которые после затвердевания бетона удаляют. Железобетонное перекрытие устанавливается готовым. [12]
В процессе бетонирования колодца ставят ерши для кронштейнов и серег или же местах, где они должны быть установлены, вставляют деревянные пробки, которые после затвердевания бетона удаляют. Железобетонное перекрытие устанавливают готовым. [13]
В процессе бетонирования захватки днища на поверхность бетона после его уплотнения и заглаживания укладывают деревянные щиты из досок толщиною 40 — 50 мм, размерами в плане 800 X 1000 мм. На нижней поверхности каждого щита укреплены электроды из стальной полосы сечением 40 X 4 мм. Соседние электроды подключают к разным фазам сети специального понизительного трансформатора для электропрогрева бетона. [14]
Фундаментные болты фиксируют в процессе бетонирования с помощью шаблона или кондуктора, которым пользуются при приемке фундамента. [15]
Страницы: 1 2 3 4 5
www.ngpedia.ru
Технология производства бетонных работ
⇐ ПредыдущаяСтр 5 из 51 Опалубочные работы
Опалубка – временная вспомогательная конструкция, обеспечивающая заданные геометрические размеры и очертания бетонного элемента или конструкции, в которую укладывают бетонную смесь. Она состоит из несущих, поддерживающих и формообразующих элементов. Основное назначение опалубки – придать необходимую форму бетонной смеси до ее затвердения и достижения бетоном требуемой прочности после распалубки.
Устанавливают и демонтируют опалубку в соответствии с проектом про-
изводства работ и инструкцией по ее эксплуатации. Выполнение опалубочных работ должно производиться в соответствии с проектом. Он включает в себя схему организации работ в увязке с другими процессами, график бетонирования и оборачиваемости комплекта опалубки на отдельных захватках или конструкциях, технологические карты на производство работ, маркировочные чертежи отдельных часто повторяющихся и сложных конструкций.
Опалубку ленточного фундамента выполняют со ступенчатым уширением книзу Для опалубки используют мелкоразмерные щиты, прогоны, схватки и крепежные детали.
Опалубку ленточного фундамента ступенчатого сечения собирают по двум технологическим схемам. По первой схеме устанавливают опалубку нижней ступени и бетонируют. Затем на затвердевший бетон ставят опалубку второй ступени и т. д. По схеме (рис) собирают опалубку на всю высоту фундамента: сначала устанавливают маячные щиты нижней ступени, которые объединяют схватками и крепежными элементами, затем устанавливают рядовые щиты и прикрепляют их к схваткам 9. Положение низа щитов фиксируют с помощью вставок и деревянных или инвентарных клиньев. На верхний пояс щитов первого яруса укладывают балки 2, которые крепят накладками. На балки 2 наносят риски с указанием расположения внутренней плоскости щитов второго яруса. По рискам устанавливают продольные схватки 3, к которым крепят щиты верхнего яруса 4 и объединяют их схваткой 5 верхнего яруса. Между собой щиты соединяют пружинными скобами, кляммерами и шпонками. Затем устанавливают через 3…4 м временные распорки и стяжки 6, которые обеспечивают заданный размер фундамента по высоте. Для устойчивости системы щиты второго яруса раскрепляют подкосами 7 с винтовыми домкратами.
Фундаменты значительной протяженности разбивают на отдельные захватки. Разбирают опалубку в обратном порядке. Собирают и разбирают опалубку для ленточного фундамента два опалубщика 4-го и 2-го разрядов.
2. Арматурные работы
Монолитные железобетонные конструкции армируют каркасами, сетками или отдельными стержнями.Плоские и пространственные каркасы изготовляют на арматурных заводах или цехах и поставляют на строительную площадку в комплекте. При небольших объемах допускается вязка или сварка каркасов из отдельных арматурных стержней на месте возведения сооружения или в непосредственной близости от него, но обязательно в зоне действия монтажного крана. При армировании массивных конструкций сварными сетками их стыкуют нахлесточным соединением или путем установки дополнительных стыковых сеток с перепуском концов арматуры, равным 30…50 ее диаметрам, но не менее 250мм. Большой объем арматурных работ занимают вертикальные конструкции (фундаменты). Их армируют, как правило, пространственными или плоскими каркасами (блоками). Монтаж таких арматурных изделий состоит из следующих технологических операций: разгрузка и подача изделий непосредственно в сооружение или на площадку временного складирования; установка в проектное положение с временным раскреплением их сваркой или растяжками; установка в проектное положение и окончательное соединение стыков сваркой; проверка выполненных работ и сдача их мастеру или производителю работ.
3. Бетонные работы
При транспортировании от бетонного завода до строящегося объекта бетонная смесь должна сохранить свои свойства: однородность, показатели подвижности и жесткости. Чтобы предотвратить расслоение и сохранить технологические свойства смеси при транспортировании, соблюдают ряд требований: перевозят ее в специальном транспорте по дорогам с жестким покрытием без выбоин и неровностей. Допускаемая продолжительность транспортирования, как правило, не должна превышать времени начала схватывания цемента. Этот параметр для обычных бетонов и бетонов на пористых заполнителях находится в диапазоне 45… 120мин. Кроме того, время транспортирования зависит и от температуры бетонной смеси: 45мин – при температуре бетона 20…30°С, 90мин – при 10…20°С и 120мин – при 5…10°С.
Технологический процесс бетонирования состоит из подготовительных, вспомогательных и основных операций.
Подготовительные операции. Перед приемом бетонной смеси подготавливают территорию объекта, подъездные пути, настилы, места разгрузки бетона, емкости для приема бетона. С помощью геодезических и мерных инструментов проверяют положение опалубки, арматуры, закладных деталей и анкерных болтов, наличие фиксаторов толщины защитного слоя бетона, устойчивость арматурных каркасов и элементов опалубки.
Вспомогательные операции. Арматуру, закладные детали и анкерные болты очищают от грязи и от отслаивающейся ржавчины. Резьбовую часть анкерных болтов предохраняют от загрязнения: смазывают солидолом и устраивают защитные трубки.
Чтобы бетон не вытекал, щели между стальными и фанерными щитами опалубки конопатят паклей или заделывают планками, шпатлюют или наклеивают полосы из специальной клеящей ленты. Распылителем, кистями или валиками наносят специальные смазочные материалы на прилегающую к бетону поверхность опалубки для снижения сцепления с ней бетона и повышения качества лицевых поверхностей бетонируемой конструкции.
Основные операции. Укладывают смесь слоями в соответствии с указаниями проекта производства работ, при этом толщина каждого слоя должна быть не более глубины проработки вибратора.
При приготовлении, транспортировании и укладке бетонная смесь чаще всего находится в рыхлом состоянии; частицы заполнителя расположены неплотно и между ними есть свободное пространство, заполненное воздухом. Назначение процесса уплотнения обеспечить высокую плотность и однородность бетона. В основном бетонную смесь уплотняют вибрированием. Под действием вибрирования частицы заполнителя приходят в колебательное движение, бетонная смесь как бы разжижается, приобретает повышенную текучесть и подвижность. В результате она лучше распределяется в опалубке и заполняет ее, включая пространство между арматурными стержнями. Продолжительность вибрирования зависит от типа вибратора и технологических характеристик бетонной смеси: чем меньше подвижность уплотняемой смеси, тем более длительной вибрации она требует. Основными признаками достаточного уплотнения являются, прекращение оседания бетонной смеси, появление на ее поверхности цементного молока и прекращение выделения пузырьков воздуха.
Глубинные вибраторы предназначены для уплотнения бетонных смесей с показателем жесткости до 10 с и осадкой конуса 5…6см при возведении монолитных армированных и неармированных конструкций, фундаментов, колонн, балок и до 30 с – при изготовлении продукции сборного железобетона. При бетонировании больших объемов массивных сооружений применяют мощные вибраторы со встроенным двигателем, а также подвесные – тяжелого типа.
Перед началом бетонирования проверяют соответствие опалубки проекту, положение арматуры, закладных деталей, геометрические размеры опалубки, ее прочность и устойчивость, наличие приспособлений для безопасного и удобного ведения работ. За час до укладки бетона металлические щиты смазывают специальными составами. Укладывают бетонную смесь горизонтальными слоями, причем она должна плотно прилегать к опалубке, арматуре и закладным деталям сооружения. Слои укладывают в одном направлении и одинаковой толщины. Последующий слой укладывают только после соответствующего уплотнения предыдущего. Для получения однородной степени уплотнения необходимо соблюдать расстояние между каждой постановкой вибратора. Оно не должно превышать 1,57R; где R – радиус действия вибратора. Толщину бетонируемого слоя устанавливают из расчета глубины вибрационной проработки: 30…50 см при ручном вибрировании и до 100см при использовании навесных вибраторов и вибропакетов.
Продолжительность укладки каждого слоя не должна превышать время схватывания в предыдущем слое. В каждом конкретном случае время укладки и перекрытия. При уплотнении укладываемого слоя глубинный вибратор должен проникать на 10… 15см в ранее уложенный слой и разжижать его. Этим достигается более высокая прочность стыкового соединения слоев.
Высота ступенчатых фундаментов под колонны промышленных зданий в зависимости от глубины их заложения может достирать 3м и более. При высоте фундаментов до 3м их бетонируют слоями. Первоначально заполняют опалубку ступенчатой части фундамента. Бетонную смесь подают бадьями или бетононасосом с рабочего настила. Каждый слой прорабатывают вибраторами. Открытые поверхности ступеней защищают щитами, что исключает утечку смеси, особенно при ее вибрировании. Затем продолжают укладку бетонной смеси в подколонник.
Закончив цикл бетонирования, открытые поверхности бетона заглаживают мастерками или лопатами.
infopedia.su
Процесс бетонирования в строительстве
В промышленном и гражданском строительстве бетонирование производится при помощи многоразовых опалубок. Они могут быть из ламинированной фанеры или других подходящих материалов. В целях свободного отделения опалубки от застывшего бетона, на ее внутреннюю поверхность наносят опалубную смазку или эмульсию. При строительстве частных объектов в качестве опалубки используют доски, плотно выстеленные пленкой или рубероидом. Важно следить, чтобы опалубка перед заливкой была чистой, сухой и свободной от снега.
Существует несколько способов доставки бетона в опалубку. Итак, бетон может подаваться:
• с лотка миксера сразу в опалубку, при условии минимального расстояния между емкостью с бетоном и местом его выгрузки
• по желобу требуемой длины — при этом скорость стекания бетона зависит от степени его подвижности, угла наклона желоба и вспомогательных механических усилий (бетон с низкой подвижностью продвигается медленнее и тяжелее)
• посредством автобетононасоса — в этом случае целесообразно использовать бетон с добавками для повышения текучести
• посредством колокола – наполняемой бетоном и поднимаемой краном над местом выгрузки емкости с открывающимся сливным отверстием на дне
Для бетонирования фундаментов лучше использовать первый и второй способы, а автобетононасос и колокол более эффективны при возведении стен, монолитных плит перекрытий, колонн и т.п.
Стадия, следующая за выгрузкой бетона – его уплотнение. Оно проводится с помощью специального вибратора путем последовательной обработки всего объема бетонной массы. Эффект вибрирования вызывает эффект уплотнения бетона как по глубине, так и по поверхности, с удалением воздушных пустот, неизбежно возникающих в процессе выгрузки. В случае отсутствия вибратора применяют штыкование бетонной массы куском арматуры.
После уплотнения бетонной массы ее следует выровнять в соответствии с задачей проекта. Для этого используют специальные технологии выравнивания. Например, протягиваются шнуры внутри опалубки, а при заливке плит перекрытий часто используют так называемые «маяки», роль которых играют куски арматуры, образующие требуемые параметры плоскости.
После заливки, уплотнения и выравнивания бетонной массы необходимо выполнить ряд условий для доведения бетона до нужной кондиции. Застывающую массу следует оберегать от слишком быстрого высыхания в теплое время, зимнего замерзания или осадков. В качестве простейшего средства защиты может быть использован плотный полиэтилен. Но в минусовые температуры этого недостаточно, и бетон приходится прогревать с помощью подключения электродов или любыми другими доступными средствами. Трехдневного прогревания бетонной массе достаточно, чтобы дойти до критической степени прочности в 50%, после чего риск разрушения или трансформации резко снижается. Жара также противопоказана застывающему бетону. Помимо пленочной или тентовой защиты залитая бетоном площадь нуждается в ежедневном орошении водой в течение недели.
Демонтаж опалубки фундамента производят на 3 или 4 день после заливки. Для перекрытий этот срок дольше – необходимо дождаться, пока конструкция не достигнет уровня прочности 80%.
n-sd.ru
Специальные методы бетонирования
Торкретирование — это нанесение на поверхность опалубки, бетона или железобетона под давлением сжатого воздуха одного или нескольких слоев цементно-песчаного раствора (торкрета).
Его применяют для устройства гидроизоляции, защитного слоя предварительно напряженной навиваемой арматуры, укрепления тонкостенных конструкций, замоноличивания швов, при ремонтных работах и исправлении дефектов в бетоне и железобетоне.
Комплект оборудования для торкретирования:
1 – компрессор, 2 – воздушные шланги, 3 – воздушный фильтр, 4 – цемент-пушка, 5 – шланг для подачи сухой смеси, 6 – сопло, 7 – торкретируемая поверхность, 8 – шланг для воды. 9 – бак
Оборудование для торкретирования включает в себя цемент-пушку, компрессор, шланги для воды и воздуха, воздушный и водяной фильтры, сопла, бак для воды.
Сжатый воздух под давлением 0,2…0,25 МПа подается от компрессора 1 по воздушным шлангам 2 в воздушный фильтр 3, где очищается от пыли, масла и других включений.
Очищенный воздух подается в цемент-пушку 4, которую предварительно загружают сухой смесью песка и цемента.
Сухая смесь далее направляется по шлангу 5 в сопло 6 и одновременно вода из бака 9 под давлением 0,35…0,5 МПа также подается в сопло для увлажнения смеси.
Увлажненная смесь со скоростью 100 м/с вылетает из сопла в виде веерообразного факела.
Частицы песка, покрытые цементной пленкой, сталкиваются с опалубкой или железобетонной конструкцией и прилипают к ней.
Вследствие высоких скоростей движения смеси имеющийся избыток химически несвязанной воды в полете удаляется с частиц.
Таким образом на поверхности постепенно наращивается слой песчаного бетона, причем частицы песка проникают в ранее нанесенный слой и уплотняют его.
Получается плотная структура бетона, которая обладает низкой водопроницаемостью и высокой прочностью.
За один цикл наносят торкретный слой толщиной 25…30 мм.
При многослойном торкретировании время между нанесением каждого слоя определяют экспериментальным путем.
Ранее нанесенный торкрет должен обладать достаточной прочностью и в то же время пластичностью для восприятия динамической нагрузки при нанесении последующего слоя.
Для торкретирования используют чистый песок влажностью не более 6% и модулем крупности 2,5…3.
Включения зерен размером более 8 мм не допускаются.
В качестве вяжущего применяют цемент марки 500 и выше, а для создания водонепроницаемых оболочек и ремонта железобетонных конструкций — быстротвердеющие цементы.
Чтобы получить плотный слой торкрета равномерной толщины, сопло при нанесении держат на расстоянии 0,7… 1 м от торкретируемой поверхности (перемещают его круговыми движениями), а струю смеси направляют перпендикулярно ей.
На вертикальные, наклонные и криволинейные поверхности торкретный слой наносят снизу вверх, чтобы свеженанесенный торкрет не сползал с них.
Регулируют вязкость смеси дозированием подачи воды.
Толщину наносимого слоя контролируют по маякам.
Потолки и вертикальные поверхности торкретируют в несколько слоев, а полы — сразу на всю толщину.
Перед торкретированием поверхность очищают сжатым воздухом и увлажняют.
Первый раз наносят слой торкрета снизу на высоту 1,3..1,5 м.
При нанесении последующих слоев зоны их перекрытия должны быть не менее 20 см.
Вышележащие слои наносят с передвижных или стационарных подмостей.
После нанесения первого слоя бетон выдерживают и при этом увлажняют.
В жаркую погоду поверхность торкретного слоя накрывают брезентом или пленочным покрытием, исключающим быстрое испарение влаги.
Когда бетон наберет необходимую прочность, наносят второй слой и т. д.
Пневмобетонирование — это нанесение на поверхность пластичных бетонных смесей на мелкозернистом заполнителе.
Смеси, как правило, приготовляют централизованно на бетонном заводе или на строительной площадке в смесителе установки «Пневмобетон».
Таким способом бетонируют конструкции толщиной до 150 мм: тонкостенные покрытия куполов, оболочки, сооружения для хранения жидкостей (резервуары), плавательные бассейны, градирни, замоноличивают стыки сборных железобетонных конструкций, а также ремонтируют (восстанавливают) бетонные и железобетонные конструкции.
Уложенный этим способом бетон отличается высокими физико-механическими показателями (плотность, водонепроницаемость, морозостойкость и сцепление с различными поверхностями).
Схема установки «Пневмобетон»:
1 – скиповый подъемник, 2 – приемно-перемешивающее устройство, 3 – вибросито, 4 – растворонасос, 5 – шланг, 6 – сопло, 7 – поверхность бетонирования
Наносят бетонные смеси установкой, которая включает в себя приемно-перемешивающее устройство 2 со смесителем принудительного действия, питатель, вибросито 3 с ячейками 10×10 мм, шланги 5, воздушный трубопровод, сопло с гасителем 6 скорости движения смеси.
В качестве приемно-перемешивающего устройства 2 используют растворосмеситель СБ-97 или принудительного действия СБ-80, оборудованный скиповым подъемником 1. Транспортируют смесь растворонасосами С-683, С-684 или С-317Б с подачей 2,4…6 м3/ч, переоборудованными на прямоточную схему и снабженными дополнительной смесительной камерой.
Шланг 5 монтируют из отдельных секций с внутренним диаметром 50 или 63 мм.
На конце шланга закреплено сопло.
При вылете из сопла скорость смеси 70…90 м/с.
Конфигурация и геометрические размеры сопла зависят от вида работ, применяемых материалов и положения сопла по отношению к бетонируемой поверхности.
Расход сжатого воздуха давлением 0,7 МПа составляет 7…9 м3/мин.
До начала работ подключают установку к электросети и водопроводу, монтируют леса или передвижные подмости так, чтобы расстояние между настилом и рабочей поверхностью было 1,2…1,5 м, а высота яруса 2 м.
Для вертикальных конструкций устанавливают опалубку облегченного типа.
Щели шириной более 5 мм в опалубке не допускаются.
При нанесении смеси сопло держат перпендикулярно бетонируемой поверхности и на расстоянии 0,7…1,2 м от нее.
Бетонную смесь на вертикальные поверхности наносят снизу вверх.
Для получения равномерной толщины бетонируемой поверхности соплом совершают спиралеобразные поступательные движения.
Для создания нормальных условий твердения бетон предохраняют от воздействия ветра и прямых солнечных лучей, ударов, сотрясений и других механических воздействий, периодически его увлажняют.
7.2 Раздельное бетонирование
При раздельном бетонировании сначала укладывают крупный заполнитель, а затем нагнетают в него (инъецируют) раствор.
При возведении массивных монолитных конструкций сначала устанавливают опалубку, затем внутри нее монтируют арматурное заполнение и инъекционные трубки.
Заполняют опалубку щебнем двух фракций: до 100 (50…60%) и до 20 мм (40…50%).
При этом каждый слой вибрируют, чтобы получить более плотную структуру бетона.
Подают щебень в опалубку бадьями.
По окончании укладки щебня к инъекционным трубкам поочередно подключают растворонасос, с помощью которого закачивают цементно-песчаный раствор.
Инъекционные трубки в нижней части на длине 0,25…0,5 м имеют перфорированные отверстия.
Раствор под давлением 0,15… 0,2 МПа заполняет пространство между частицами щебня.
Схема раздельного бетонирования массивных фундаментов:
1 – опалубка фундамента, 2 – инъекционные трубы, 3 – щебеночная засыпка, 4 – область распространения раствора
Рассмотрим технологическую схему раздельного бетонирования массивных фундаментов.
Инъекционные трубки устанавливают на таком расстоянии друг от друга, которое обеспечивает взаимное пересечение зон их действия не менее чем на половину радиуса действия.
Раствор нагнетают непрерывно до полного заполнения пространства между щебнем, о чем свидетельствует появление в контрольных отверстиях, оставляемых в щитах опалубки, раствора.
Затем трубы поднимают на высоту 1… 1,5 м и процесс нагнетания повторяют.
При возведении фундаментов большой высоты после бетонирования одного-двух ярусов инъекционные трубки укорачивают путем исключения их звеньев.
Технология бетонирования тонкостенных конструкций имеет свои особенности.
Прежде всего в конструкции опалубки предусмотрено двустороннее расположение отверстий 4 в шахматном порядке для инъекции раствора.
Схема раздельного бетонирования тонкостенных конструкций:
1 – опалубка, 2 – арматурное заполнение, 3 – крупный заполнитель, 4 – отверстия для ннъекции раствора, 5 – инъектор, 6 – контрольное отверстие, 7 – металлическая спираль
Первоначально в опалубку 1 устанавливают арматурное заполнение 2 и одновременно укладывают крупный заполнитель 3 фракции 40…20 мм слоями и уплотняют его вибраторами.
Высота каждого слоя должна быть на уровне отверстий для инъекции. После укладки очередного слоя крупного заполнителя устанавливают металлические спирали 7, которые служат направляющими при движении раствора от инъектора.
Перед бетонированием крупный заполнитель смачивают водой.
Инъектор 5 направляют в отверстие 4 опалубки.
Раствор под давлением 0,15…0,2 МПа распространяется сначала по спирали 7, а через пространство между ее витками — в заполнитель. Момент окончания нагнетания определяют по появлению раствора в контрольных отверстиях 6.
Процесс бетонирования, как правило, ведут с двух сторон двумя инъекторами снизу вверх.
Такой метод обеспечивает получение плотного водонепроницаемого бетона независимо от степени его армирования.
При раздельном бетонировании упрощается технологическая схема укладки бетона, снижаются транспортные расходы, повышается качество работ, но усложняется контроль качества работ и повышаются требования к конструкции опалубки (должна быть жесткой без щелей и неплотностей).
7.3 Подводное бетонирование
Подводное бетонирование — укладка бетонной смеси под водой без применения водоотлива — применяют при возведении подводных частей опор мостов, днищ опускных колодцев и других массивных сооружений на глубине 1,5…50 м. Бетонную смесь к месту укладки в основном подают двумя способами.
Способ вертикально перемещающихся труб (ВПТ) основан на непрерывной подаче бетонной смеси по вертикально расположенной трубе, которую по мере увеличения толщины бетонного слоя поднимают с помощью кранов и лебедок так, чтобы нижний конец трубы всегда находился в толще бетона.
Расстояние между трубами зависит от их диаметра, подвижности бетонной смеси и интенсивности бетонирования. В среднем для труб диаметром 200…300 мм их радиус бетонирования около 6 м.
При этом расстояние между трубами должно быть 10…11 м.
Схема подводного бетонирования способом вертикально перемещающихся труб:
1 – опалубка, 2 – рабочий настил, 3 – звенья труб, 4 – загрузочная воронка, 5 – вибраторы, 6 – стойка, 7 – бетоновод, 8 – плавучий кран
При подводном бетонировании трубы 3 устанавливают с рабочего настила 2.
Каждую трубу собирают из секций длиной 1…1,2 м.
Верхняя секция оканчивается загрузочной воронкой 4, на одну из сторон которой навешивают вибратор 5.
Смесь от бетононасоса по бетоноводу 7 поступает непрерывно и заполняет весь объем трубы.
Затем смесь под гидростатическим давлением вытекает из нижнего отверстия трубы.
Чтобы предотвратить размыв бетона, низ трубы должен быть погружен в бетон на глубину 0,5…0,8 м.
Таким образом, свежие порции бетона как бы вытесняют ранее уложенный и не контактируют с водой.
По мере роста толщины бетонной подушки трубу постепенно извлекают и лишние секции демонтируют. Бетонирование считается оконченным, когда уровень бетона дойдет до проектной отметки.
Бетон подают непрерывно. При перерывах, больших, чем время схватывания цемента, ухудшается монолитность конструкции.
Способ восходящего раствора (ВР) является разновидностью раздельного бетонирования.
Он состоит в нагнетании с помощью растворонасосов 10 в каменную наброску или гравийно-щебеночную отсыпку 1 цементного раствора 2 с осадкой конуса 10…12 см.
Для этой цели устанавливают решетчатые шахты 6, в которые пропускают трубы 7 для нагнетания по ним раствора.
Радиус действия каждой трубы 2…3 м.
Схема подводного бетонирования способом восходящего раствора:
1 – каменно-щебеночная отсыпка, 2 – раствор, 3 – штунтовое ограждение (опалубка), 4 – ограждение, 5 – настил, 6 – шахта, 7 – труба, 8 – лебедка, 9 – рукав, 10 – растворонасос
При нагнетании раствор, выходя из нижнего конца трубы, поднимается вверх и, вытесняя из пустот воду, заполняет их. Так создается бетонный монолит.
По мере повышения уровня раствора в шахте трубы поднимают, оставляя нижний конец трубы длиной 0,8…1 м в растворе.
Подводное бетонирование методом втрамбования
Втрамбовывание бетонной смеси начинают с создания бетонного островка в одном из углов бетонируемой конструкции при подаче смеси по трубе или в бадьях с открывающимся дном.
Островок должен возвышаться над поверхностью воды не менее чем на 30 см.
Для втрамбовывания применяют бетонную смесь подвижностью 5…7 см.
Подводный откос островка, с которого начинают втрамбовывание, должен образовывать под водой угол 35…45° к горизонтали.
Новые порции бетонной смеси втрамбовывают в островок равномерно с интенсивностью, не нарушающей процесс твердения уложенного бетона, и не ближе 20…30 см от кромки воды.
Этим приемом обеспечивается защита от соприкосновения с водой новых порций бетонной смеси.
Метод применяют при глубине воды до 1,5 м для конструкций больших площадей при классе бетона до В25.
Метод укладки кюбелями. Бетонную смесь опускают под воду на основание бетонируемого элемента в кюбелях (раскрывающихся ящиках, бадьях или грейферах) и разгружают через раскрытое дно или затвор.
Обычно применяют кюбели вместимостью от 0,2 до 3,0 м3, закрытые сверху и имеющие уплотнения по контуру раскрывания, которые препятствуют вытеканию цементного теста и проникновению воды внутрь кюбеля.
Бетонную смесь выпускают при минимальном отрыве дна кюбеля от поверхности уложенного бетона, исключая тем самым возможность свободного сбрасывания бетонной смеси через толщу воды.
Преимущество метода укладки кюбелями заключается в возможности бетонирования на любой глубине, в производстве работ без подмостей, в возможности укладки бетонной смеси на неровное основание с большими углублениями и возвышениями.
Однако при бетонировании кюбелями происходит частичный размыв смеси при разгрузке кюбеля и появляется некоторая слоистость укладки.
Этот метод применяют, если марка укладываемого бетона не выше 200.
Укладку бетонной смеси в мешках следует рассматривать как вспомогательный метод, который применяют при небольших объемах работ, для уплотнения щелей между дном и опалубкой, а также в аварийных случаях.
Бетонную смесь, укладываемую в мешках из редкой, но прочной ткани готовят на щебне с крупностью заполнителя 40 мм и осадкой конуса 2-5 см. объем смеси в одном мешке 10…20 л.
Мешки со смесью укладывают водолазы, тщательно прижимая их один к другому.
7.4 Основы технологии полимерцементных бетонов и пластбетонов
Полимерцементным бетоном называют искусственный каменный материал, связующими которого являются полимер и цемент, заполнителями — песок и щебень.
В отличие от обычных бетонов с модифицирующими добавками (ГКЖ-94, винсол), которые из-за малых количеств практически не меняют структуру бетона, содержание полимера в полимерцементных бетонах достаточно велико.
Это позволяет получать материалы с новыми свойствами.
Они имеют меньшую массу, морозостойки, обладают несколько большей прочностью по сравнению с обычными, повышенной износостойкостью.
Полимерцементные бетоны получают тремя способами:
— введением в бетон при смешивании водных дисперсий полимеров (поливинилацетата или синтетического каучука), распадающихся в бетонной смеси с выделением воды, при этом обезвоженный полимер выполняет роль дополнительного связующего;
— добавлением в воду затворения водорастворимых мономеров и полимеров (фуранового и поливинилового спиртов, эпоксидных, фенолформальдегидных смол и т. п.) с последующим их отверждением в бетоне нагревом или с помощью отвердителей;
— пропиткой бетона на необходимую глубину маловязкими полимерами (карбамидами, лаком «этиноль», стиролом), которые отверждаются непосредственно в бетоне.
Заполнителями для полимерцементных бетонов служат кварцевые или дробленые пески, а также щебень прочных и плотных горных пород крупностью не более 20 мм.
Применяют также полимерцементные мелкозернистые растворы.
Оптимальное содержание полимера типа поливинилацетата составляет от 15 до 20% к массе цемента в пересчете на сухое вещество.
При этом наилучшим образом используются свойства как цемента, так и полимера.
При такой дозировке в полимерцементном бетоне сохраняется сплошность цементного геля, а полимер, обволакивая цементные сростки и зерна заполнителя, дополнительно склеивает их.
При увеличении полимера сплошность цементных новообразований нарушается, из-за чего снижается прочность полимерцементных бетонов.
Оптимальное содержание водорастворимого карбамидного полимера С-89, а также эпоксидных полимеров ДЭГ-1 и ТЭГ-17 около 2% по отношению к массе цемента.
При этом водоцементное отношение бетонной смеси можно понизить до 0,29 — 0,30 без ущерба для ее удобоукладываемости, а также стойкости в агрессивных средах.
Применяя различные полимерные составляющие, можно получить полимерные бетоны, стойкие к действию нефтепродуктов, жиров и растворов солей.
Полимерцементные бетоны применяют для устройства износоустойчивых полов, аэродромных покрытий, резервуаров под нефтепродукты, а также монолитных конструкций для работы в агрессивных средах.
Для приготовления полимерцементных смесей применяют лопастные мешалки или вибросмесители.
При механическом перемешивании смесь насыщается воздухом, в бетоне образуются мелкие поры, равномерно распределенные по объему.
Вследствие того, что полимерцементные бетоны применяют пока в небольших объемах, их смеси готовят в смесителях, расположенных вблизи места укладки.
Полимерцементные смеси обладают повышенной вязкостью, поэтому виброуплотнять их при низких частотах (3000 кол/мин) малоэффективно.
Воздух не удаляется из бетона, структура его получается чрезмерно пористой и рыхлой.
Более целесообразно высокочастотное вибрирование, а для жестких смесей трамбование и вибропрессование.
Полимерцементные бетоны, приготовленные на водных дисперсиях полимеров, выдерживают в воздушно-сухих условиях, бетоны же с добавками эпоксидных и карбамидных полимеров быстро твердеют во влажных условиях.
Пластбетоны — искусственные конгломераты, получаемые целиком на органических полимерных связующих. Они являются, по существу, пластмассами с минеральными наполнителями различной крупности.
Связующими в пластбетонах служат маловязкие термореактивные полимеры (фенолформальдегидные, фурановые, полиэфирные и эпоксидные), которые при добавлении отвердителей и в определенных условиях твердеют, склеивая компоненты в прочный конгломерат.
Обычно применяют пластбетоны составов 1:5-1:15 (полимер : наполнитель по массе).
Для отверждения полимеров применяют керосиновый контакт Петрова, сульфокислоты и минеральные кислоты, полиэтиленполиамин, диэтилентриамин и др.
В качестве наполнителей применяют чистые пески с крупностью зерен 0,6-2,5 мм и содержанием глинистых и пылеватых частиц не более 0,5%.
Щебень и гравий должны быть сухими и чистыми и иметь крупность не более 20 мм.
Помимо гранитного щебня в качестве наполнителей применяют андезитовый и баритовый, а также измельченный трепел и графит в зависимости от назначения пластбетона.
Прочностные свойства пластбетонов определяются свойствами связующего и наполнителя, а также адгезией между ними.
Пластбетоны обладают высокой прочностью, особенно при растяжении и изгибе.
Так, прочность при изгибе некоторых пластбетонов на эпоксидных полимерах достигает 350…450 кгс/см2.
Пластбетоны практически водонепроницаемы, морозостойки; они хорошо сопротивляются износу, стойки в агрессивных средах.
Например, стойкость их против действия кислот в 10 раз выше, чем у обычных бетонов.
Пластбетоны целесообразно применять для гидроизоляционных и антикоррозионных облицовок.
Их используют для получения износоустойчивых полов, в аэродромных покрытиях, а также для возведения частей зданий и сооружений, эксплуатируемых в агрессивных средах.
Пластбетонные смеси готовят в небольших объемах непосредственно у мест их укладки из-за быстрого их твердения.
В лопастный смеситель загружают наполнители, затем полимерные связующие.
После 3…4 — минутного перемешивания и получения однообразной массы вводят отвердитель и перемешивают в течение 5…8 мин.
Приготовленную порцию смеси сразу же укладывают в дело.
Уплотняют ее трамбованием или штыкованием.
Твердеют пластбетоны лучше в сухих условиях при 50…100° С.
Повышение относительной влажности выше 60% снижает прочность пластбетонов, особенно на полиэфирных полимерах.
Составы на эпоксидных полимерах менее чувствительны к повышенной влажности.
Время прогрева уложенных пластбетонов составляет 4…8 ч в зависимости от вида полимера и состава смеси.
При твердении пластбетонов происходит их усадка, величина которой зависит от вида и количества полимера.
perekos.net